The gas filter separator, known in Arabic as فاصل مرشح الغاز, represents a pivotal component in the natural gas processing industry, ensuring the purity and safety of the end product. This article delves into the intricacies of gas filter separators by providing insights that stand out in their depth, thus enhancing your understanding and ensuring your operational decisions are both informed and authoritative.
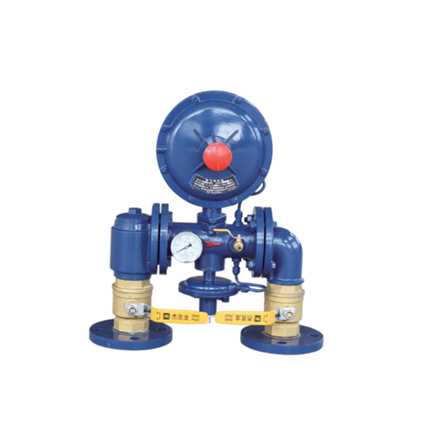
In essence, a gas filter separator is designed to efficiently remove solid particulates and liquid mists from gas streams, ensuring that the gas reaching the end user is of the highest quality. This is particularly critical in industries where gas purity is non-negotiable and where operational inefficiencies can lead to significant economic losses.
To appreciate the expertise and technological advancements behind these devices, it's instrumental to consider how they operate.
Gas filter separators typically employ a two-stage process to enhance the filtering efficiency. The first stage involves the use of a filter element tasked with capturing solid particles; these may include dust, rust, or other debris that could otherwise damage downstream equipment. The second stage is a coalescer element that removes liquid mists from the gas stream, such as water or hydrocarbon liquids, ensuring that only dry, pure gas is transported further along the processing system.
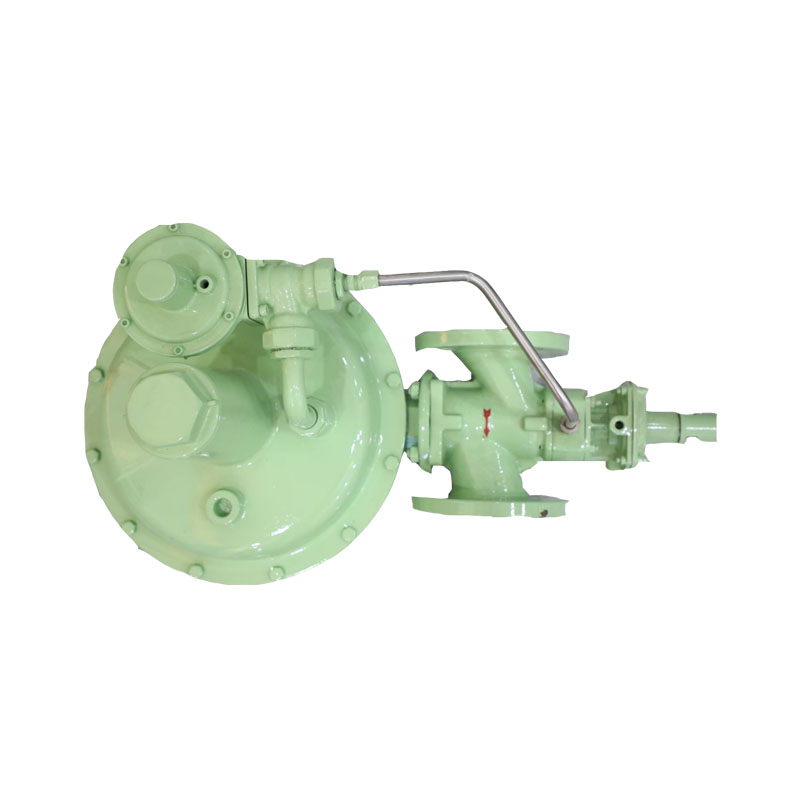
From an operational standpoint, selecting the right gas filter separator necessitates a thorough understanding of various factors including the nature of the gas stream, the specific contaminants to be removed, and the operational conditions under which the separator will function. It's a confluence of experience and expertise — marrying one's knowledge of gas filtration specifications with real-world operational scenarios.
The authority of a gas filter separator is often reflected in its design and material composition, aspects that are crucial for those selecting and maintaining these systems. For instance, the choice of materials for construction can significantly influence the separator's durability and efficiency. High-performance applications may require stainless steel construction to combat corrosion and withstand extreme pressures, while effective sieve configurations within the separator enhance the interception and coalescing of undesired particulates.
Gas filter separation
Incorporating a trustworthy gas filter separator into your system can yield not only operational efficiencies but also significantly enhance safety protocols. A reliable separator mitigates the risk of equipment failure or shutdowns, events that are invariably costly. Moreover, regulatory compliance often mandates certain filtration standards, and a well-specified separator can help in meeting and even exceeding these regulatory barriers.
The real-life application of gas filter separators unfolds across diverse scenarios. Consider the experience of an oil and gas processing facility facing consistent issues with liquid carryover, leading to frequent compressor shutdowns. By integrating a high-caliber gas filter separator, the facility not only resolved carryover issues but also extended the lifetime of downstream equipment, underscoring the separator's role in preventive maintenance.
The gas filter separator is not merely a component but a testament to the importance of precision and foresight in industrial gas processing. As advancements in technology continue to unfold, staying abreast of emerging separator models and their configurations will be crucial for industry professionals who seek to maintain excellence in operations.
In conclusion, the reliable performance of gas filter separators hinges on a blend of profound technical understanding and the strategic application of that knowledge. A grasp of the nuances in design and application can significantly contribute to both operational efficiency and the continuous delivery of high-quality gas, ensuring that the end-to-end gas processing chain functions seamlessly, safely, and sustainably.