Basket strainers are essential components in numerous industrial and commercial applications. Known for their ability to filter and protect, these devices ensure the smooth operation of systems by removing unwanted debris and particles from fluids. Whether you're working with water, oil, gases, or chemicals, the right basket strainer can make a significant difference in both efficiency and maintenance costs.
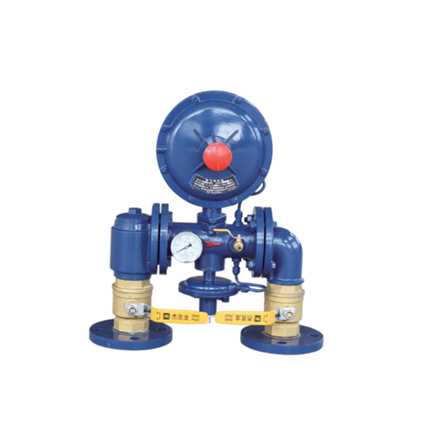
When selecting a basket strainer, it's important to consider several factors to ensure optimal performance and longevity.
The material of the strainer is a primary consideration. Stainless steel, brass, and PVC are common materials used in basket strainers, each offering unique advantages. Stainless steel is renowned for its strength and corrosion resistance, making it ideal for aggressive environments. Brass offers excellent heat resistance, while PVC is suitable for lighter applications where cost-effectiveness and chemical resistance are paramount.
The size and design of the basket strainer also play crucial roles in its performance. Strainers come with varying mesh sizes, which determine the size of particles they can filter out. Fine mesh strainers are excellent for trapping small debris, while coarse mesh strainers are better suited for larger particles. Additionally, the flow rate capacity should match the needs of your system to avoid pressure loss or reductions in efficiency.
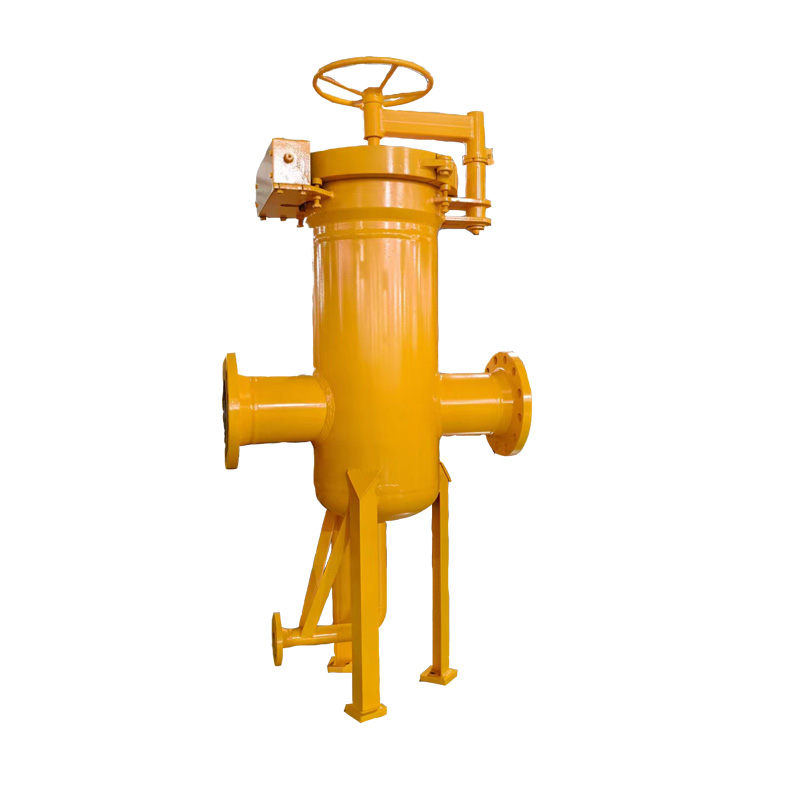
In terms of design, there are temporary and permanent strainers. Temporary strainers are used for short periods, often during start-ups, to protect equipment from damage caused by larger debris. Permanent strainers, however, are designed for long-term use, offering continuous protection.
Basket strainers not only help in prolonging the life of machinery by preventing clogging and wear but also contribute to higher quality output by ensuring only clean fluids pass through. This is particularly crucial in industries like pharmaceuticals and food processing where contamination control is critical.
basket strainers
Installation and maintenance are other vital aspects of basket strainer management. Proper installation ensures that the strainer functions correctly, while regular maintenance checks can prevent potential failures. It is crucial to follow the manufacturer's guidelines for cleaning and replacing the baskets to maintain optimal performance.
Advanced basket strainers today come with features such as automatic cleaning or backwashing capabilities, minimizing the need for manual intervention and reducing downtime. These smart strainers are increasingly adopted in industries seeking to enhance efficiency and reliability in their processes.
The expertise involved in selecting and maintaining a basket strainer underlines its importance in maintaining operational excellence. Consultations with experienced engineers or the strainer's manufacturers can provide invaluable insights into the best practices for choosing and using these devices. Such guidance ensures that the strainers are not only integrated seamlessly into your system but also operate at their best capacity throughout their lifespan.
In conclusion, basket strainers are indispensable in maintaining the efficiency and safety of fluid-handling systems across various sectors. Investing in quality basket strainers and their maintenance can result in significant savings and longer equipment lifespans, underscoring the critical nature of these seemingly simple devices. With advances in design and technology, basket strainers continue to evolve, offering even greater performance and reliability, solidifying their place as essential components in modern industry.