Relief valves are pivotal components in various industrial and commercial applications, ensuring systems operate safely and efficiently. These valves play a crucial role in protecting equipment and personnel by maintaining pressure levels within specified limits. Understanding their utility, selection criteria, and maintenance can significantly enhance operational reliability and safety.
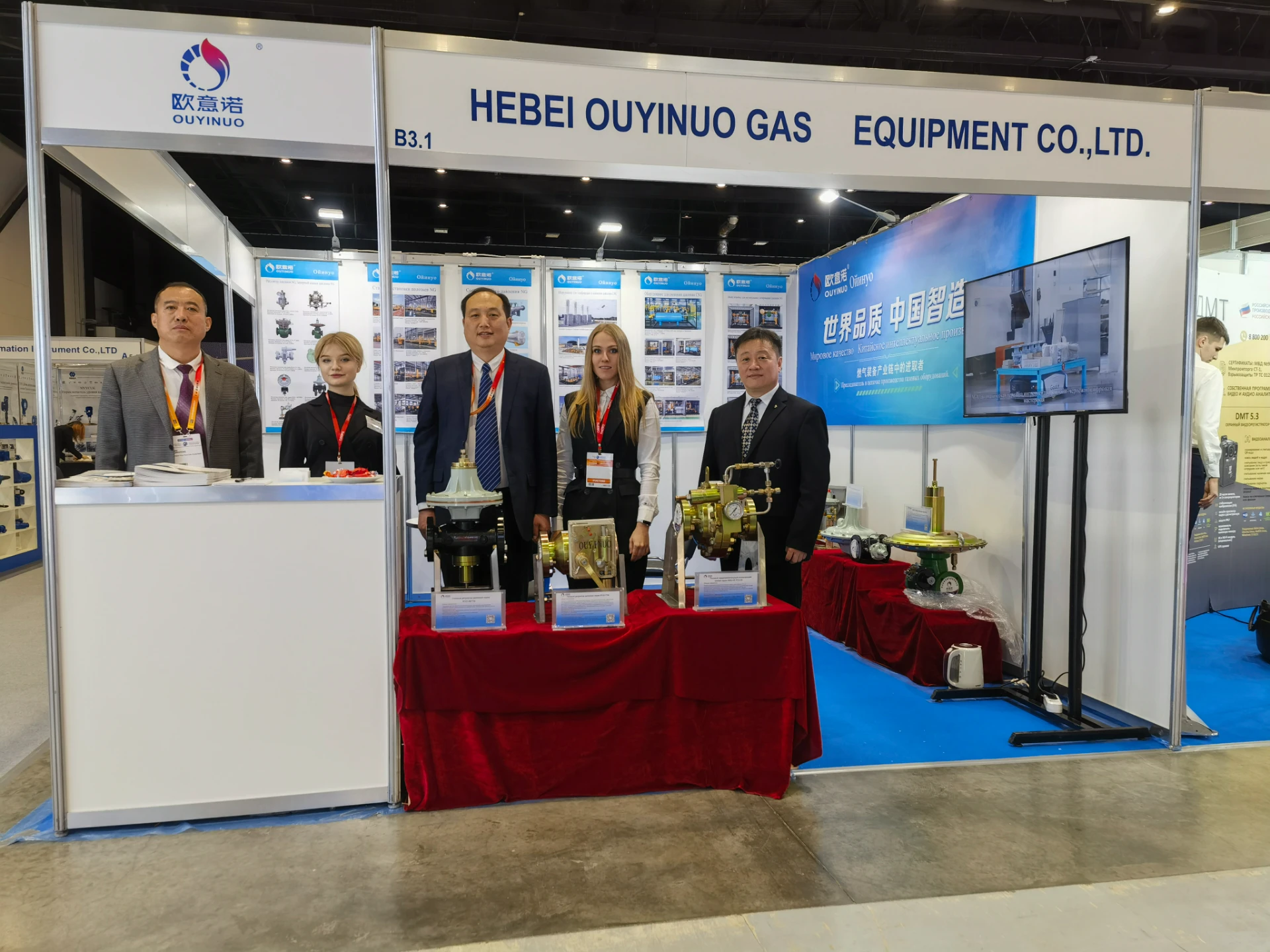
A relief valve operates by providing an outlet for fluid, typically gas or liquid, once the pressure exceeds a preset level. This mechanism prevents potential system overpressure scenarios which can result in catastrophic failures. Their versatility spans across different sectors, including oil and gas, manufacturing, chemical processing, and even in household appliances like water heaters.
Choosing the right relief valve requires a nuanced understanding of the system's operational dynamics. Key factors to consider include the set pressure, back pressure, temperature conditions, and flow rate requirements. These parameters dictate the valve's design,
materials, and functionality. For instance, in corrosive environments, a valve made from stainless steel or Hastelloy offers superior durability and performance. Meanwhile, in high-temperature applications, materials that can withstand elevated conditions without degrading are essential.
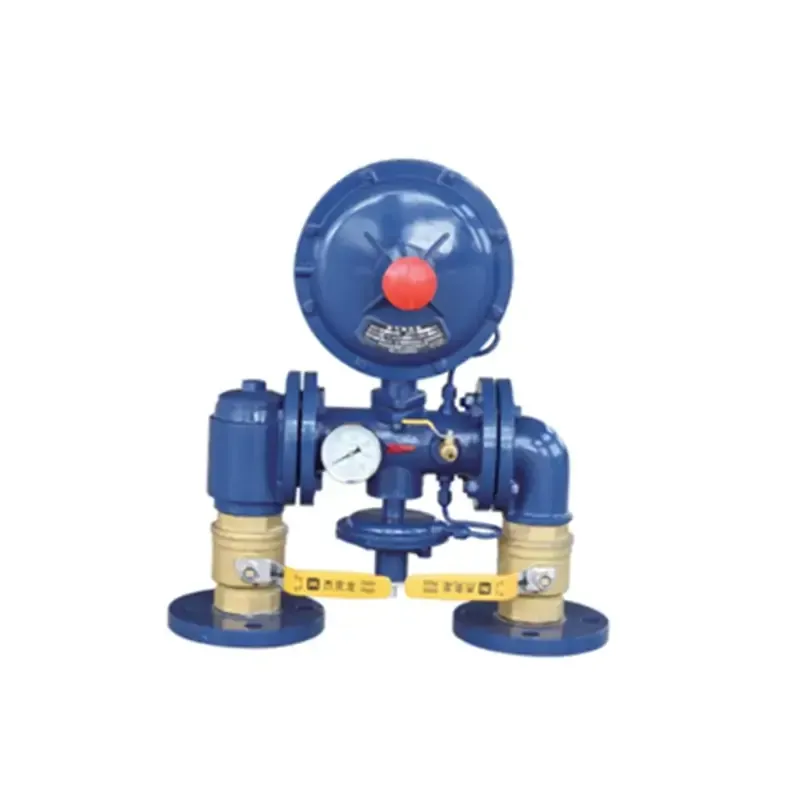
The design of relief valves varies from spring-loaded and pilot-operated to balanced-bellows types, each suitable for different applications. Spring-loaded relief valves are common in situations requiring rapid response to pressure excesses, while pilot-operated valves are preferred for systems needing precise control and minimal pressure fluctuations. Balanced-bellows valves provide an edge in systems with variable back pressure, maintaining stability in valve operation.
relief valves
Regular maintenance and inspection are critical for ensuring long-term functionality and safety of relief valves. A well-maintained valve will respond accurately to pressure changes, reducing the risk of system downtime or accidents. Routine checks should include visual inspection for leaks or damage, pressure testing to confirm operational set points, and cleaning to prevent blockages from debris or corrosion deposits. Engaging skilled professionals to conduct these inspections guarantees adherence to industry standards and enhances system reliability.
The importance of adherence to industry standards and codes cannot be overstated. Standards such as the American Society of Mechanical Engineers (ASME) Boiler and Pressure Vessel Code provide comprehensive guidelines for the design, manufacturing, testing, and maintenance of relief valves. Compliance with these standards ensures the valves perform optimally under specified conditions and offer maximum safety.
Furthermore, leveraging technological advances can enhance the effectiveness of relief valves. Innovations like smart sensors and monitoring systems provide real-time data on valve performance, facilitating predictive maintenance and immediate response to pressure anomalies. This integration of technology not only optimizes operational efficiency but also significantly reduces the risk of unexpected system failures.
In conclusion, relief valves are integral to the safe and efficient functioning of various systems across industries. Their selection and maintenance require a deep understanding of operational conditions and compliance with relevant standards. By prioritizing these elements, businesses can safeguard their operations against pressure-related risks, thereby ensuring continuity and protection of valuable assets. Investing in quality relief valves and cutting-edge monitoring solutions is a strategic decision for companies aiming for sustainable growth and operational excellence.