Navigating the intricacies of gas metering can be a daunting task, but with the right guidance, it transforms from a complex technical challenge to an intuitive process that optimizes your resource management. Gas metering is essential in various industries, as it plays a crucial role in measuring the volume and flow of gas, ensuring accuracy in billing, and safeguarding energy efficiency. Here, we delve into the profound intricacies of gas metering and how advances in technology are steering it into a new era of precision and reliability.
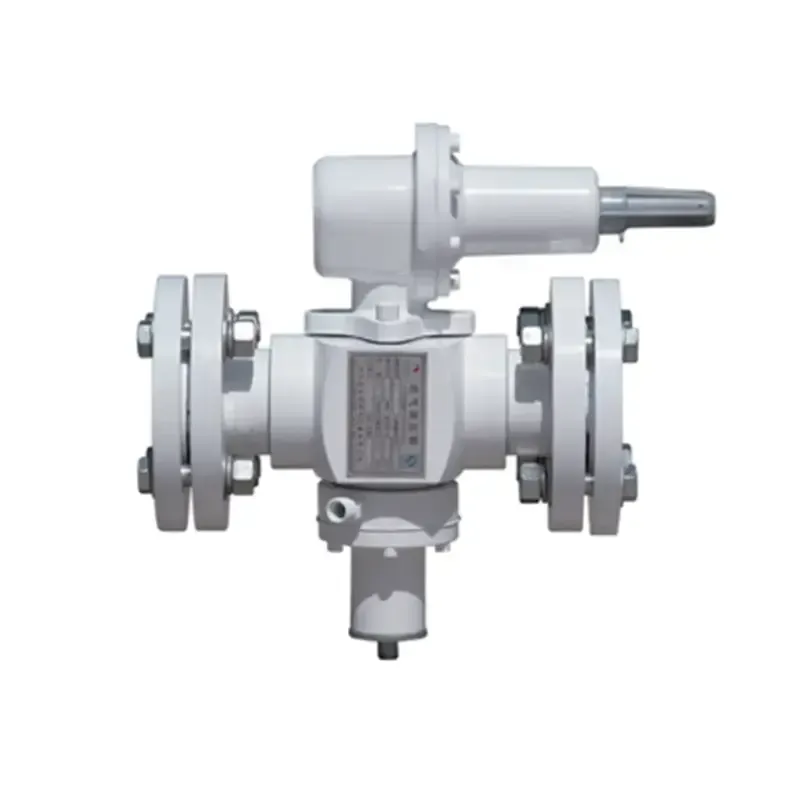
At its core, gas metering involves devices designed to measure and record the amount of gas passing through a particular point. Different methodologies are employed in gas metering, each with its distinct benefits and suitability to specific applications. Among these, the most common types are diaphragm meters, rotary meters, turbine meters, and ultrasonic meters. The choice of meter hinges on several factors, including the specific application, the type of gas, and the required precision.
Diaphragm meters are often favored for residential and small business use due to their simplicity and cost-effectiveness. These meters work by using a complex series of internal chambers and diaphragms that expand and contract as gas flows through, allowing for accurate measurement.
Their robustness and ease of use make them a reliable choice for many small-scale applications.
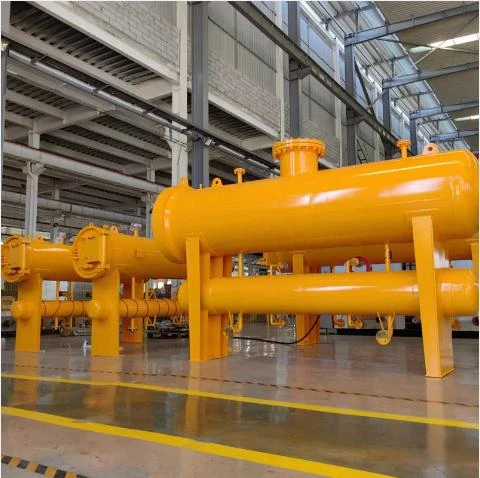
For commercial and industrial settings where higher volumes of gas flow are involved, rotary meters often reign supreme. They measure gas by rotating impellers inside a precisely machined chamber, capable of handling large flow rates with impressive accuracy. This makes them indispensable in industries where precision and efficiency are paramount.
Turbine meters, on the other hand, are prized for their high accuracy and are commonly deployed in circumstances requiring meticulous measurement of fast-moving gases. They work through a rotation mechanism, where gas flow turns a turbine and the revolutions are proportional to the volume of gas passing through. These meters are integral in both pipeline and plant operations, offering precision measurement that is crucial for safe and economic management of resources.
gas metering
Stepping into modern gas metering technology, ultrasonic meters are considered the pinnacle of advanced metering solutions. They utilize ultrasonic sound waves to measure gas flow, providing unparalleled accuracy, versatility, and a non-invasive method of measurement. These meters are ideally suited for high-pressure and high-volume measurement scenarios, making them essential in the evolving landscape of gas management.
The importance of precise gas metering cannot be overstated. As governments and organizations worldwide push for stricter regulations on emissions, accurate gas metering becomes a vital tool in achieving and maintaining compliance. Innovations in gas metering technology have not only enhanced reliability but also integrated smart technologies that allow for real-time monitoring and data analysis.
Additionally, the incorporation of Internet of Things (IoT) technology in gas metering systems represents a paradigm shift, enabling remote tracking and management of gas flow data. This diminishes the necessity for manual readings, reducing human error, and improving operational efficiency. IoT-equipped gas meters provide instant data analytics, paving the way for proactive maintenance and operational optimization.
In conclusion, gas metering has evolved significantly, encompassing features that boost accuracy, reliability, and operational efficiency. Selecting the right gas meter requires an understanding of specific needs, potential working environments, and the technological benefits each type offers. With continuous advancements on the horizon, industries across the board can anticipate even greater precision, adaptability, and integration capabilities, reinforcing the indispensable role of effective gas metering in global resource management.