In the complex realm of industrial design and manufacturing, gas pressure vessels stand as crucial components with diverse applications. These essential containers are employed to store gases at a pressure considerably different from the ambient pressure, making their expertise-driven design and manufacturing a priority for several industries including petrochemical, energy, and transportation.
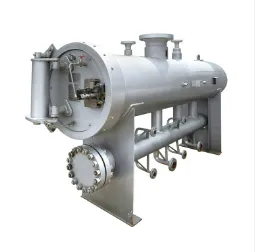
Experience dictates that understanding material science is fundamental when approaching gas pressure vessel production. Steel and composite materials are the industry’s choice due to their durability, fatigue resistance, and cost-effectiveness. Expertise in these materials allows for optimizing the vessel’s performance while ensuring safety under extreme conditions. Over the years, advancements in composite materials engineering have introduced lighter, corrosion-resistant options, offering enhanced efficiency.
Industrial professionals must stay abreast of these developments to maintain a competitive edge.
Authoritativeness in designing gas pressure vessels necessitates adherence to stringent regulations and standards. Governing bodies like the American Society of Mechanical Engineers (ASME), European Union Pressure Equipment Directive (PED), and others establish codes that ensure vessels' safety, reliability, and efficiency. Having in-depth knowledge of these standards is non-negotiable for manufacturers aiming to penetrate global markets. ASME’s Boiler and Pressure Vessel Code, for instance, lays out meticulous design, construction, and testing procedures to uphold safety, thus reinforcing an entity’s authoritative standing in the industry.
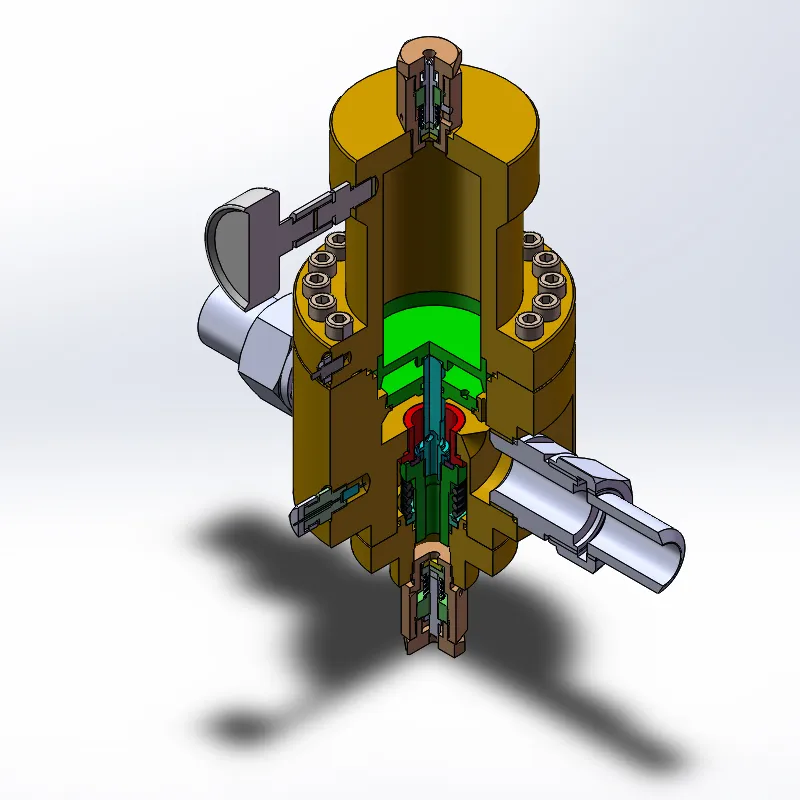
Trustworthiness is further built through rigorous testing and validation processes. Each pressure vessel must undergo careful inspection, including non-destructive testing (NDT) methods such as ultrasonic, radiographic, and magnetic particle inspections. Adopting state-of-the-art hydrostatic and pneumatic testing practices certifies that pressure vessels can withstand operational stress without failure. Companies that invest in comprehensive testing not only ensure compliance but also instill confidence in prospective clients, solidifying their reputation as trustworthy partners in the supply chain.
gas pressure vessel
Strategically, implementing cutting-edge technologies like Finite Element Analysis (FEA) in the design phase can predict performance under various conditions, thereby fostering further trust. This software-driven approach allows engineers to evaluate and improve design flaws, reducing the likelihood of material failure. A secure track record in research and development, underscored by practical experience, elevates any supplier’s status as an expert and a reliable authority in the field.
To harness a sustainable approach, contemporary trends focus on greener manufacturing processes for gas pressure vessels. Recyclable materials, energy-efficient production methods, and initiatives to reduce carbon footprints align with the global thrust towards sustainability. Expert knowledge in integrating eco-friendly practices into the traditional manufacturing paradigm not only decreases environmental impact but also aligns with consumer demands, bolstering market position.
In conclusion, maintaining a strategic focus on experience, expertise, authoritativeness, and trustworthiness is paramount in the gas pressure vessel industry. Emphasizing these pillars not only ensures compliance with international standards but also enhances operational safety and fosters enduring client relationships. Future growth and sustainable innovation depend on these foundational principles, paving the way for continued advancement in gas pressure vessel technology.