Gas pressure vessels stand as a pivotal component within numerous industries, offering a vital service in ensuring the safe and efficient handling of gases under pressure. Their construction requires profound expertise, underpinned by rigorous standards to ensure safety and reliability. This article delves into the essential aspects surrounding gas pressure vessels, highlighting key factors that underscore their importance in industrial applications.
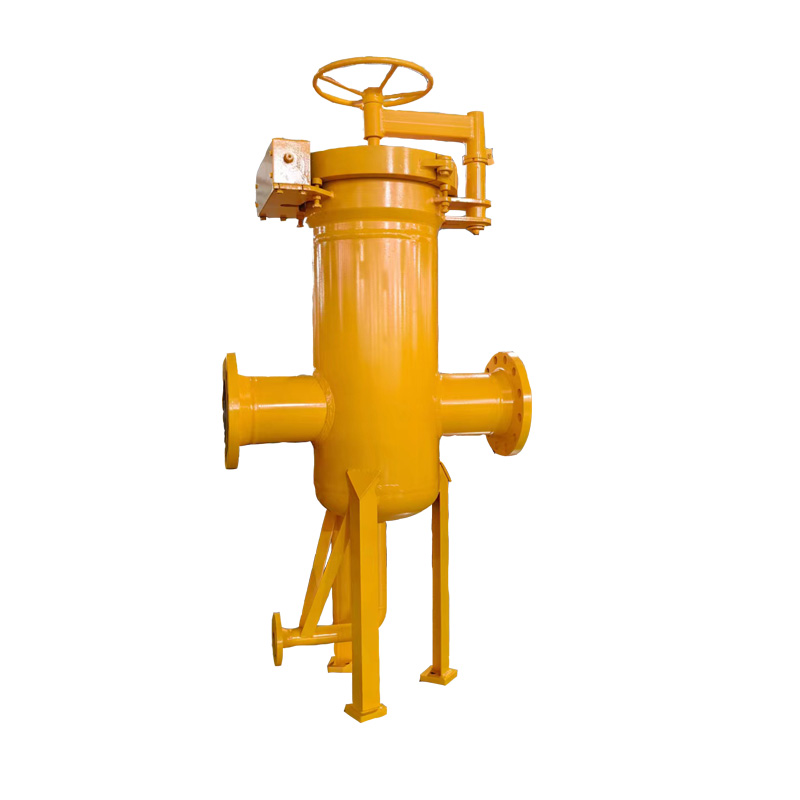
The design and fabrication of gas pressure vessels demand a high degree of specialization. Engineers must account for a multitude of factors, including the type of gas stored, operating pressures, temperature conditions, and environmental considerations. Materials used must exhibit exceptional strength and corrosion resistance to withstand internal pressures and external environmental impacts. Common materials include high-strength carbon steel, stainless steel, and sometimes advanced alloys, each selected based on specific application needs.
Safety is non-negotiable in the operation of gas pressure vessels. Meticulous adherence to industry standards such as ASME BPVC Section VIII or the European PED (Pressure Equipment Directive) is compulsory. These standards guide the design, manufacturing, testing, and maintenance processes, ensuring that vessels can endure the strains of constant use. This ensures that unexpected events, such as overpressure or fatigue, do not lead to catastrophic failures.
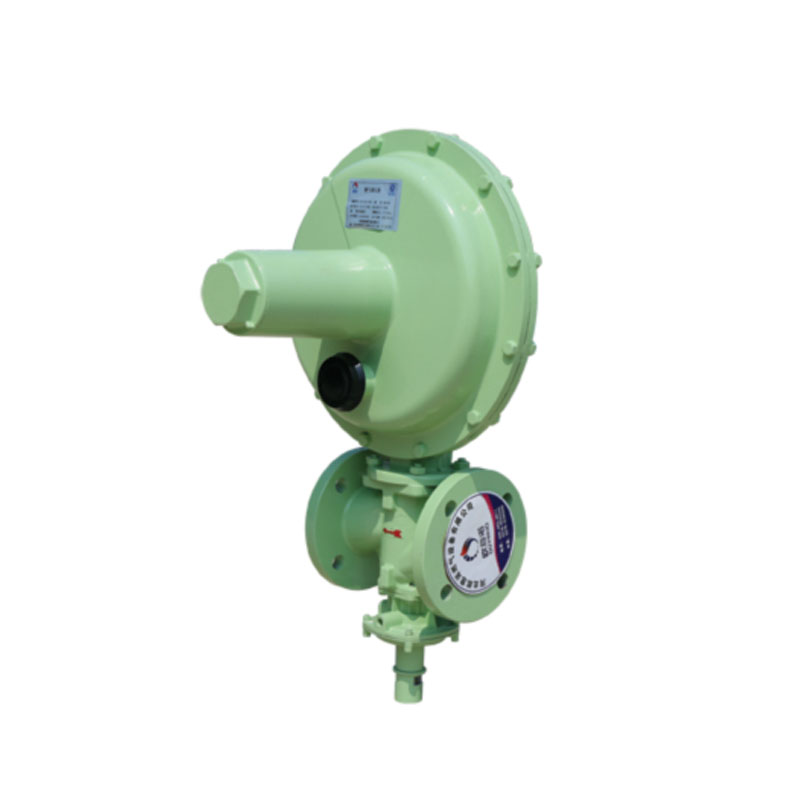
From a practical experience standpoint, routine inspections and periodic maintenance are pivotal in extending the life of a gas pressure vessel. Non-destructive testing methods such as ultrasonic testing, radiography, and magnetic particle inspection are employed to detect any potential defects before they lead to failure. Real-world experience shows that early detection and remediation of such issues significantly reduce downtime and operational costs.
gas pressure vessel
Expertise in gas pressure vessel management extends beyond design and maintenance. It involves understanding the specific requirements of the application. For example, vessels used in the chemical industry may encounter more corrosive environments than those used in natural gas storage. Therefore, the selection of materials and protective coatings is critical to ensuring longevity and operational efficiency.
The authority that surrounds manufacturers of gas pressure vessels is often demonstrated through certifications and a proven track record in delivering quality solutions. Leading manufacturers invest in state-of-the-art technology, such as automated welding processes and computer-aided design (CAD) systems, to enhance precision and efficiency in vessel production. This authoritative approach not only streamlines production but also assures clients of a product that meets stringent safety and quality benchmarks.
Trustworthiness in this domain is built on transparency and robust customer service. Manufacturers establish long-term relationships with clients by offering comprehensive lifecycle support, including installation, maintenance, and emergency response services. Providing detailed documentation and user training helps end-users operate the vessels safely and efficiently, reinforcing trust in the manufacturer's commitment to safety and quality.
In conclusion, gas pressure vessels are indispensable in various industrial settings, offering safe and effective solutions for handling gases under pressure. Their design and construction require specialized knowledge, adherence to stringent safety standards, and the use of high-quality materials. By combining practical experience, technical expertise, authoritative manufacturing practices, and trustworthy customer service, the industry ensures that these critical components continue to serve their purpose efficiently and safely, thereby empowering the operations they support.