Gas pressure vessels play an indispensable role in industries ranging from energy production to chemical processing. Their intricate designs and critical functions necessitate a profound understanding of their operation and safety protocols. This article delves into the intricacies of gas pressure vessels, drawing from both industry expertise and real-world experience to highlight their importance and functionality.
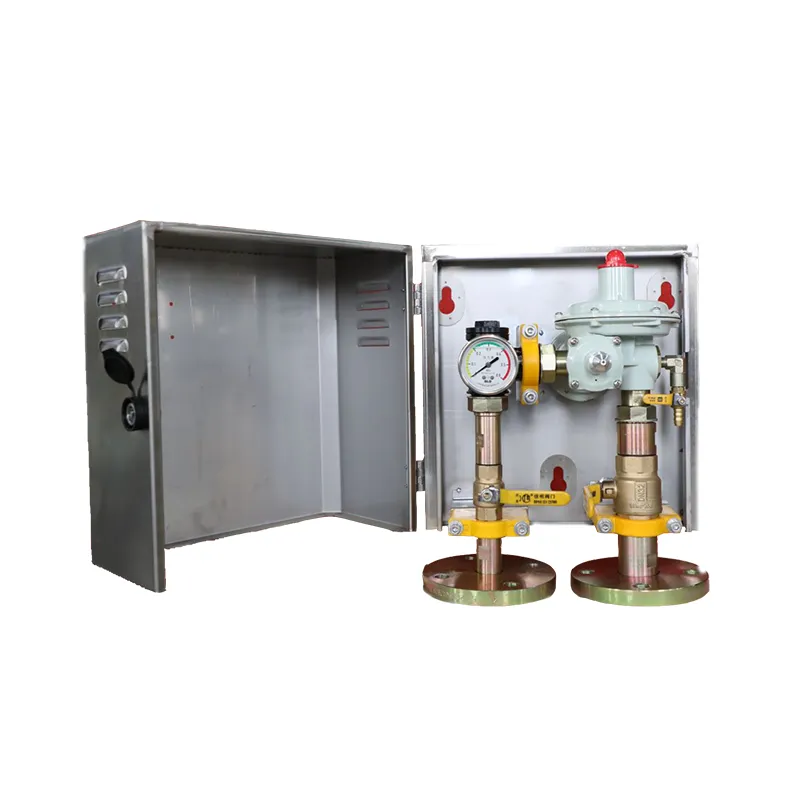
A gas pressure vessel is essentially a container designed to hold gases or vapors at a pressure significantly different from the ambient pressure. Their construction and maintenance demand a high level of expertise due to the inherent risks associated with pressurized gases. The vessels are typically made from robust materials like stainless steel or aluminum alloys, chosen for their resilience under stress and resistance to corrosion.
From a technical standpoint,
expertise in materials science and engineering is crucial for constructing pressure vessels. Engineers must consider factors such as tensile strength, thermal conductivity, and fracture toughness when selecting materials. In addition, the design must align with stringent regulatory standards, such as the ASME Boiler and Pressure Vessel Code, which dictates safety margins and testing procedures.
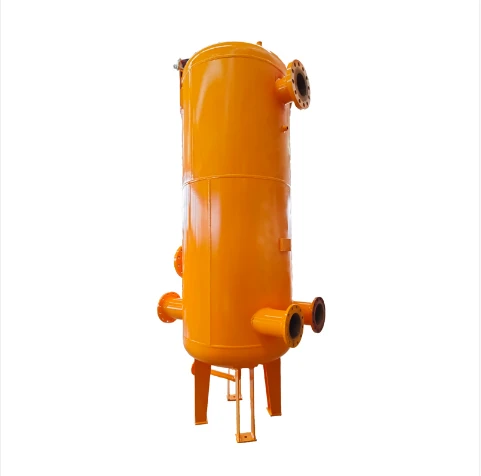
Real-world experience underscores the importance of rigorous testing and maintenance protocols. Regular inspections can prevent catastrophic failures by identifying potential issues such as corrosion, fatigue cracking, or external damage. Non-destructive testing methods, like ultrasonic testing or radiography, are often employed to ensure the integrity of the vessel over its lifespan.
Authoritative knowledge in thermodynamics and fluid mechanics is also vital for understanding the behavior of gases under pressure. High-pressure gas can change state rapidly, and understanding these thermodynamic principles is crucial for both operating and designing pressure vessels safely. Moreover, experts often employ advanced simulation software to model the stress distribution and flow dynamics, ensuring that the design meets all operational requirements.
gas pressure vessel
Trustworthiness in the context of gas pressure vessels hinges on adherence to safety standards and transparency in manufacturing processes. Trusted manufacturers will provide documentation detailing the material properties, design specifications, and quality assurance tests conducted during production. This transparency not only builds trust with clients but also ensures compliance with international standards.
In terms of practical application, gas pressure vessels are used in various sectors. In the energy industry, they store and transport gases like hydrogen and natural gas. Chemical industries use them in reactors and separation systems. The versatility of these vessels is attributed to their ability to handle a wide range of temperatures and pressures, making them suitable for numerous industrial processes.
Furthermore, technological advancements are continually enhancing the safety and efficiency of gas pressure vessels. Innovations in composite materials offer lighter, stronger alternatives to traditional metals. Smart sensors can monitor pressure and temperature in real-time, providing data that can preemptively signal for maintenance or alert of potential risks.
In conclusion, gas pressure vessels are a vital component of many industrial processes. Their complexity requires a deep well of expertise, from material science to safety engineering. By adhering to rigorous standards and leveraging technological advancements, these vessels can operate safely and efficiently, thus maintaining their critical role in a variety of applications. The combination of expertise, experience, and a steadfast commitment to safety underlines the continuing evolution and importance of gas pressure vessels in today's industrial landscape.