For over a decade, my journey as a gas valve technician has unveiled the nuanced evolution and critical importance of gas valves in various industries. These seemingly modest components serve as the pivotal heartbeats of any gas-powered system, ensuring efficiency, safety, and reliability. As technologies advance and sectors demand increasing energy efficiencies, the intricacies of gas valve technology are rightly gaining deserved attention.
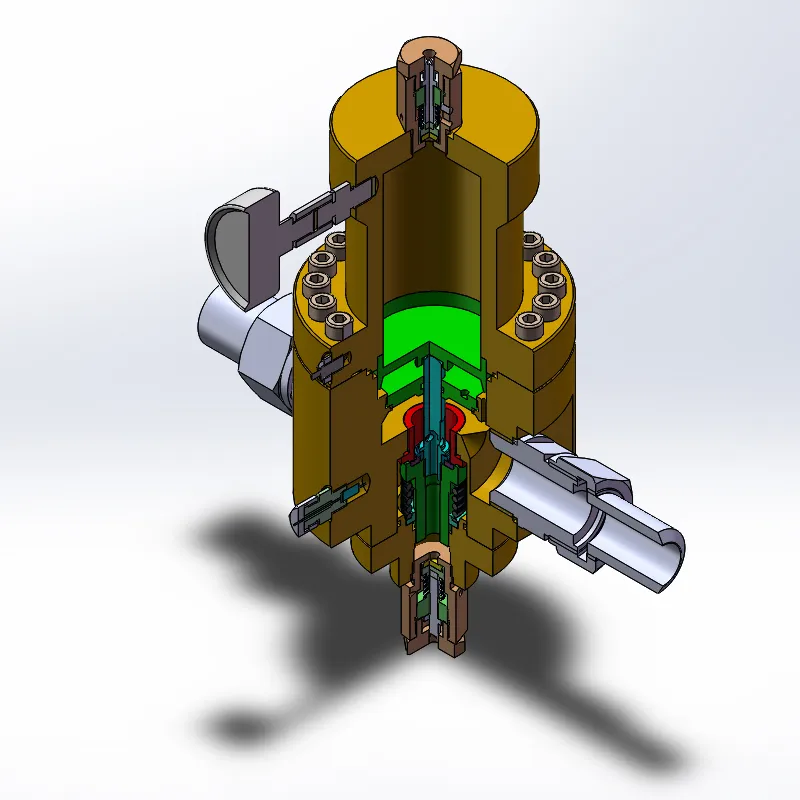
Understanding the vital role of gas valves requires delving into their primary function—controlling the flow and pressure of gas within a pipeline or system. A well-designed gas valve is crucial for maintaining system stability, preventing leaks, and optimizing fuel consumption. The selection process for a gas valve, therefore, is not just about choosing any valve but the right valve for the specific application.
From my extensive hands-on experience, selecting the appropriate gas valve hinges on several factors—pressure ratings, material compatibility, temperature range, and the type of gas being used. Investing in a suitable valve can dramatically enhance the safety standards and operational efficiency of an industrial setup. Brass and stainless steel are commonly employed due to their durability and resistance to corrosion, ensuring longevity even under harsh conditions.
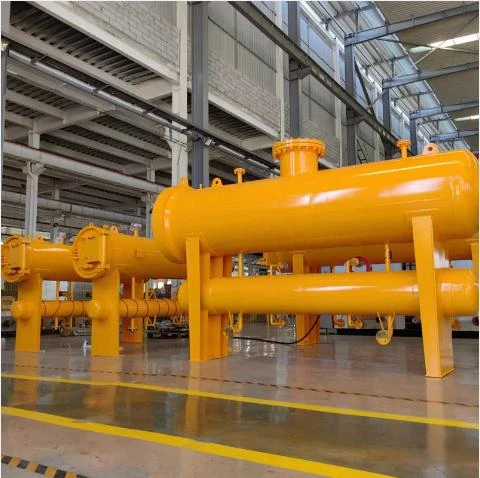
Advancements in smart technology have birthed a new generation of gas valves—equipped with IoT-enabled sensors that allow for real-time monitoring and remote adjustments. These intelligent valves not only enhance operational efficiency but also provide crucial data analytics for predicting maintenance needs, thereby reducing downtime and optimizing performance. Expertise in integrating these systems, however, requires a keen understanding of both legacy systems and new technologies.
gas valve
Authoritativeness in the realm of gas valve technology comes from staying informed about industry standards and regulations. Organizations such as the American Society of Mechanical Engineers (ASME) and the Gas Appliance Manufacturers Association (GAMA) establish stringent guidelines for valve performance and safety. Complying with these standards not only guarantees safety but also engenders trust in the system's reliability among end-users and stakeholders.
Trustworthiness in the gas valve industry is heavily reliant on consistent quality assurance and rigorous testing. Each valve must undergo thorough inspections to confirm its adherence to quality standards and its capability to handle the prescribed conditions. As someone deeply embedded in the field, I can attest to the importance of working with manufacturers who prioritize meticulous testing and demonstrate transparency in their quality assurance processes.
Gas valves may appear as mere components, but their impact on safety and efficiency is unparalleled. For businesses focusing on energy conservation, a modern gas valve's effectiveness can prompt significant reductions in fuel consumption, directly impacting operational costs. Moreover, understanding the financial impact of regulatory compliance or the lack thereof is essential—non-compliance can lead to costly fines or, worse, catastrophic failures.
In conclusion, choosing the right gas valve embodies a commitment to safety, efficiency, and technological progress. By integrating expertise, upholding stringent manufacturing standards, and adopting innovative solutions, industries can significantly enhance their operational reliability. It is this pursuit of excellence and stringent attention to detail that ensures both the safety and longevity of gas-powered systems across the globe. Embracing these practices not only safeguards operations but also fortifies a company’s reputation in the ever-evolving landscape of gas technology.