In the realm of thermal management systems, heat exchangers serve as fundamental components, playing a pivotal role in a myriad of industrial applications. These devices, designed to efficiently transfer heat between two or more fluids, are quintessential in processes where temperature regulation is paramount. Offering insights from both expert perspectives and real-world applications, this discussion delves into the multifaceted utility and benefits of heat exchangers, ensuring a seamless synthesis of theoretical knowledge and practical experiences.
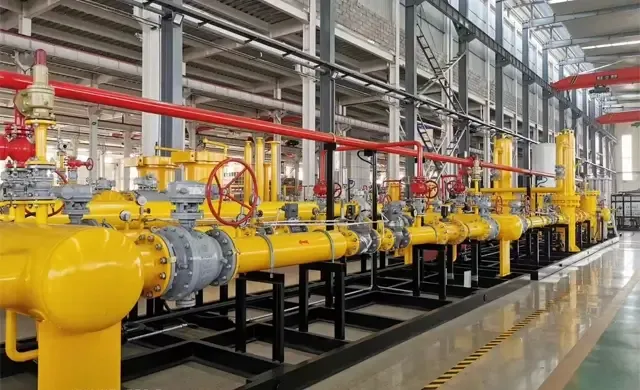
Several types of heat exchangers exist, each tailored to specific needs. The most common include shell and tube, plate, and air-cooled heat exchangers. Shell and tube models, renowned for their robustness, are extensively deployed in industries such as chemical processing and power generation. Their capacity to handle high-pressure differentials makes them a go-to choice for demanding environments. In contrast, plate heat exchangers, praised for their compact design and efficient heat transfer rates, are increasingly favored in sectors like HVAC and refrigeration. Leveraging corrugated plates to create turbulence, these exchangers facilitate superior thermal performance while maintaining a smaller footprint.
From an expertise standpoint, selecting an appropriate heat exchanger involves a deep understanding of process requirements and fluid dynamics. Key considerations include the nature of the fluids involved, the heat transfer rate required, and the operational parameters like temperature and pressure. Expertise in material science is also critical, as the choice of construction materials directly impacts the exchanger's durability and efficiency. Corrosion-resistant alloys like stainless steel are often recommended for systems exposed to corrosive substances, thus ensuring longevity and operational reliability.
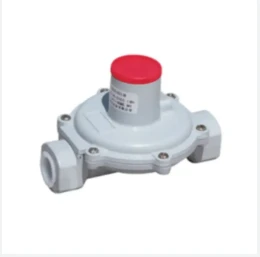
heat exchanger
Trustworthiness and authoritativeness in a heat exchanger's performance are often validated through rigorous testing and certification. Certified models, compliant with industry standards such as ASME or ISO, provide assurance regarding safety and performance metrics. Additionally,
real-world experiences highlight the importance of regular maintenance and monitoring. Organizations that integrate comprehensive maintenance protocols witness reduced downtime and optimal performance, thereby maximizing their investment in these pivotal devices.
The ongoing evolution in heat exchanger technologies underscores the significance of energy efficiency and sustainability. Advances in design, such as enhanced surface geometries and the use of nanofluids, exemplify the continuous strides toward achieving higher thermal efficiencies while minimizing energy consumption. Consequently, industries can not only reduce their carbon footprint but also achieve significant cost savings.
In conclusion, heat exchangers are indispensable tools in the arsenal of thermal management solutions. Their ability to seamlessly integrate into diverse industrial settings, coupled with ongoing advancements in technology, underscores their essential role in enhancing operational efficiency and promoting sustainable practices. By prioritizing expertise, reliability, and continuous innovation, businesses can harness the full potential of heat exchangers, ensuring optimized performance and energy conservation in their processes.