A heat exchanger stands as a cornerstone technology in various industries, pivotal for thermal management and energy efficiency. From HVAC systems in residential buildings to massive industrial processes, its applications are vast and indispensable. Understanding how these devices operate and choosing the right one for your needs involves considering numerous factors that intertwine with expertise and innovation.
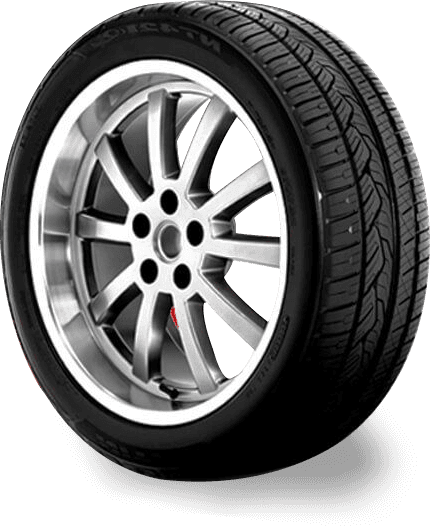
Heat exchangers exist primarily to transfer heat between two or more fluids, which may be separated by a solid wall to prevent mixing. This functionality is essential in processes where heat needs to be conserved or dissipated. For instance, in automotive engines, they help dissipate heat, ensuring optimal engine performance and longevity. In industrial settings, they recover waste heat, contributing significantly to sustainability efforts.
Broadly speaking, heat exchangers can be classified into three main types shell and tube, plate, and air-cooled designs. Each has unique characteristics tailored to specific applications.
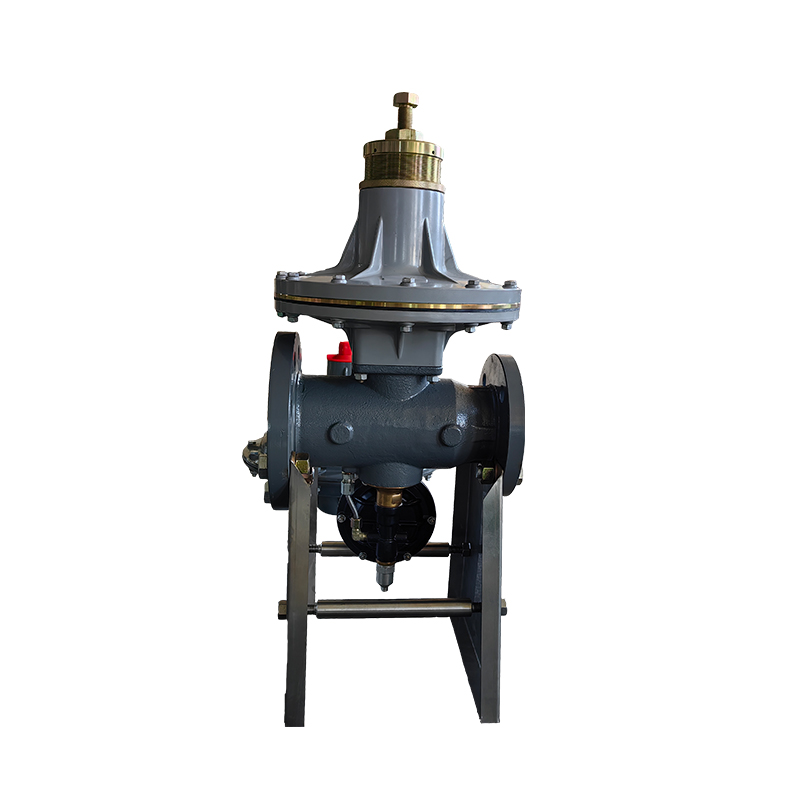
Shell and tube heat exchangers are most commonly used due to their robust design and flexibility in handling pressures and temperatures. They consist of a series of tubes, one set carrying the hot fluid and the other set carrying the cooling fluid. Their modular design allows for easy maintenance and scaling, which is why they are favored in petroleum refineries and chemical plants.
Plate heat exchangers, on the other hand, are known for their compact and efficient design, comprising numerous thin, slightly separated plates that have very large surface areas and fluid flow passages. This design maximizes heat transfer, making them ideal for applications where space is limited and efficiency is critical, such as in refrigeration and air conditioning systems.
Air-cooled heat exchangers, which use air to remove excess heat, are advantageous in environments lacking abundant cooling water. These are typical in power plants and heavy manufacturing facilities where water conservation is as critical as performance.
heat exchanger
Despite these general applications, selecting the ideal heat exchanger involves expertise. One must consider the specific thermal and flow requirements, alongside factors like fluid type, fouling tendencies, and pressure drop allowances. For instance, a food processing plant may prioritize sanitary design to prevent contamination, therefore leaning towards a plate heat exchanger with stainless steel construction.
The evolving landscape of heat exchangers is seeing innovations aimed at enhancing Experience, Expertise, Authoritativeness, and Trustworthiness in their use. Research is driving towards corrosion-resistant materials and self-cleaning mechanisms to reduce maintenance costs and downtime. Furthermore, the integration of IoT technology allows for real-time monitoring and predictive maintenance, offering enhanced performance and reliability.
Trustworthiness is a crucial factor as well. Users and industries demand products that uphold the highest safety and operational standards. Manufacturers now employ rigorous testing methodologies, ensuring heat exchangers can withstand operational stresses and comply with global standards such as the American Society of Mechanical Engineers (ASME) and the International Organization for Standardization (ISO).
Consulting with heat exchanger experts provides invaluable insights tailored to your specific application needs. These professionals offer not only technical advice but also guidance on cost-effective practices, ensuring that your investment leads to optimized energy use and reduced operational expenses.
With global challenges such as climate change and resource scarcity, the emphasis on sustainable energy solutions is more pressing. Heat exchangers play a pivotal role in this by enhancing energy efficiency and reducing carbon footprints across various sectors, from industrial manufacturing to commercial infrastructure.
In conclusion, a heat exchanger is more than a component; it is a vital part of sustainable industrial operation. Leveraging technology and expertise, industry players continue to push boundaries, ensuring these systems meet the growing demands for efficiency, environmental stewardship, and reliability. Thus, selecting the right heat exchanger becomes not just a matter of need but a strategic decision that aligns with broader goals of innovation and sustainability.