Pneumatic control valves serve as essential components in various industrial processes, playing a vital role in regulating the flow of air or gases within a system. Their efficiency and reliability are crucial for maintaining optimal performance across different sectors, including manufacturing, oil and gas, and chemical processing. This article aims to provide an in-depth understanding of pneumatic control valves, emphasizing their benefits and expert insights into their practical applications.
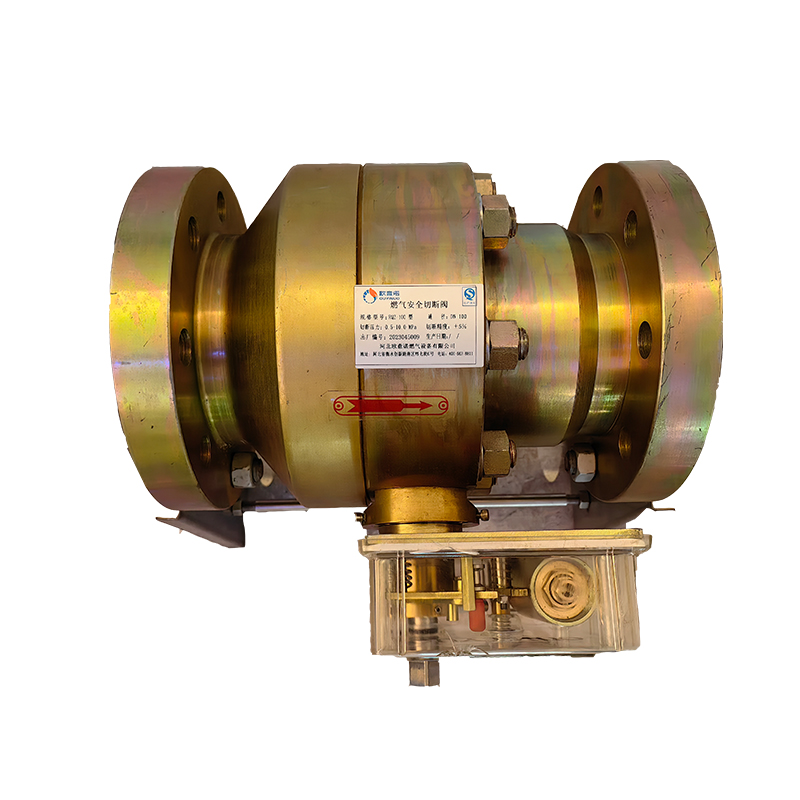
A pneumatic control valve operates by using air pressure to control the position of a valve plug or disc, which in turn regulates the flow of material through the valve. The primary advantage of pneumatic systems is their simplicity and the ability to provide precise control in harsh environments where electronic systems might fail. Moreover, they are inherently explosion-proof, making them ideal for use in industries dealing with flammable materials.
Expertise in selecting the right pneumatic control valve involves understanding the specific needs of the system it will serve. Factors such as pressure requirements, flow capacity, and material compatibility must be considered. Industry professionals recommend conducting a thorough analysis of the process conditions, including flow rate, temperature, and pressure differentials. This ensures that the chosen valve type, be it globe, butterfly, or ball, performs efficiently and reliably, minimizing downtime and maintenance costs.
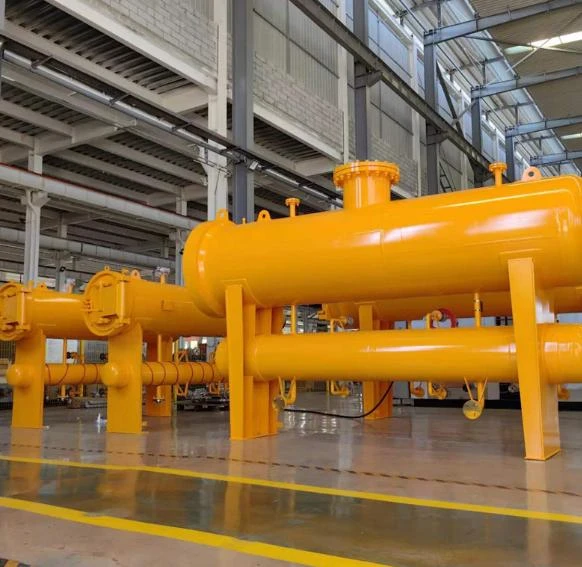
A colloquy with seasoned engineers in the field often reveals that the integration of smart technology with pneumatic systems has significantly enhanced their functionality. Modern pneumatic control valves can now be equipped with smart positioners that offer real-time diagnostics and performance monitoring. This integration allows for predictive maintenance, reducing unexpected failures and extending the valve's lifecycle – a feature that has transformed how industries approach operational efficiency and cost management.
pneumatic control valve
From an authoritative perspective, leading manufacturers continue to innovate in valve design, offering solutions that cater to specific industrial challenges. For instance, custom-engineered valves with enhanced sealing capabilities and corrosion-resistant materials are available for applications in extreme conditions, such as offshore drilling and chemical processing plants. These advancements demonstrate a commitment to quality and reliability, underscoring the industry's dedication to meeting rigorous safety and performance standards.
Trustworthiness in pneumatic control valve systems is ensured through adherence to international standards and certifications. Valves that comply with ISO, ANSI, and other industry-specific standards provide users with confidence in their performance. Regular third-party testing and certification further bolster this trust, ensuring that each valve meets the necessary safety and operational guidelines before deployment.
In practical application, real-world scenarios highlight the importance of pneumatic control valves in achieving efficient process control. A case study from a chemical manufacturing plant illustrates how the installation of high-performance pneumatic control valves resulted in a 20% increase in production efficiency. By optimizing the control of steam and gas flow, the plant not only improved its output but also reduced energy consumption, showcasing the environmental and economic benefits of well-chosen pneumatic solutions.
In conclusion, pneumatic control valves are indispensable in modern industrial processes. Through expertise in selection, integration of smart technologies, and assurance of quality and standards, these valves ensure reliable and efficient operation. As industries continue to evolve, the demand for advanced and robust control valve solutions will persist, driven by the need for safety, efficiency, and sustainability.