Pneumatic valves are pivotal components in various industrial applications, ensuring the smooth operation and control of compressed air systems. These devices leverage compressed air to actuate mechanical movements, playing a critical role in enhancing the efficiency and reliability of different systems. Their significance is underscored by their wide usage in sectors such as manufacturing, automation, and automotive industries, where precision and control are paramount.
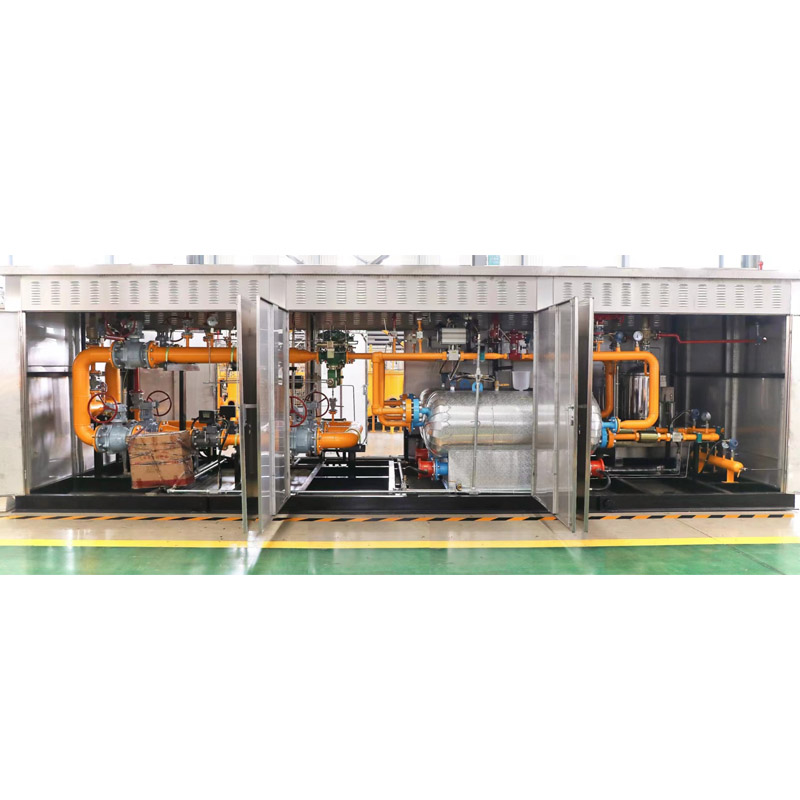
Pneumatic valves come in an array of types, each designed for specific functions and applications. The most common types include directional control valves, pressure relief valves, flow control valves, and shut-off valves. Directional control valves are arguably the most central to pneumatic systems, directing airflow to specific paths and enabling actuators to function appropriately. Their operation is critical in determining the accuracy and efficiency of motion control in various machines.
An industry-specific insight reveals that the effectiveness of pneumatic systems hinges heavily on the quality and reliability of the valves used. High-quality pneumatic valves are manufactured with precision engineering, ensuring durability and minimal maintenance requirements. As a professional in the field, it's essential to recognize the benefits of using valves that meet industry standards over cheaper alternatives that may lead to frequent replacements or system downtimes.
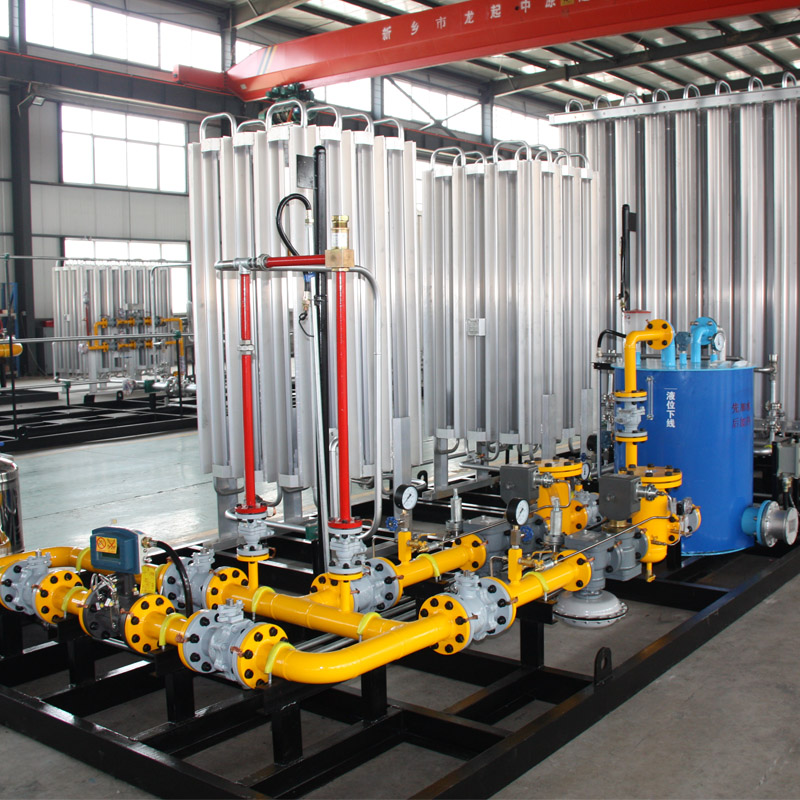
Moreover, expertise in pneumatic systems suggests that integration and compatibility are key components of successful implementations.
Pneumatic valves must seamlessly integrate with existing systems to ensure optimal performance. Industry professionals often recommend conducting a compatibility assessment before integrating new pneumatic components into existing systems. This ensures not only smooth operation but also prolongs the lifespan of the equipment.
pneumatic valve
In terms of authoritativeness, it’s crucial to note that leading manufacturers of pneumatic valves adhere to international standards such as ISO and DIN. These standards ensure that the valves are reliable, safe, and efficient. The materials used in manufacturing, such as stainless steel or brass, often determine the valve's suitability for different environments, especially those that are harsh or corrosive. Technical knowledge of the appropriate materials and standards can significantly elevate the performance of pneumatic systems and reinforce trust among end-users.
Trustworthiness in pneumatic valve systems is non-negotiable, especially in industries involving critical operations like chemical processing or food and beverage production. Trust is built through consistent performance and compliance with stringent safety protocols. Regular audits and certification from reputable bodies assure users of the valves' reliability and the manufacturer’s commitment to quality.
From a real-world experience standpoint, pneumatic valves have proven to be instrumental in energy conservation. They help manage air consumption efficiently, which translates to reduced operational costs. For instance, using a flow control valve optimizes air consumption by regulating the speed of actuators, leading to significant energy savings. A company case study showed a 15% reduction in energy costs by simply optimizing the pneumatic valve configurations across their manufacturing units.
In conclusion, pneumatic valves are indispensable in modern industrial applications. Their role goes beyond basic mechanical functions by contributing to overall system efficiency, reliability, and safety. For best results, industry experts advocate for regular maintenance and system evaluations to ensure valves are operating optimally. In the rapidly advancing technological world, staying updated with the latest in pneumatic valve technology can provide a competitive edge, enhancing productivity and ensuring long-term operational success.