Pressure vessels are a cornerstone in industrial applications, ranging from oil and gas to food processing. As a critical component, their design, manufacture, and maintenance require adherence to stringent standards and regulations to ensure safety and efficiency. Understanding the intricate balance between the operational demands and safety requirements is vital for any industry relying on pressure vessels.

Pressure vessels are built to hold gases or liquids at a pressure substantially different from the ambient pressure, necessitating a robust design and construction approach.
The expertise required begins with material selection. Common materials include carbon steel, stainless steel, and other alloys, each selected based on the application, operating temperature, and pressure conditions. Experts in metallurgy assess factors such as corrosion resistance, tensile strength, and ductility to determine the most suitable material for the given application.
The design process involves thorough expertise in engineering principles. This includes calculations for wall thickness, taking into consideration internal and external pressures as per the American Society of Mechanical Engineers (ASME) standards. Each vessel design undergoes rigorous stress analysis to predict how it will perform under various conditions, ensuring integrity and safety.
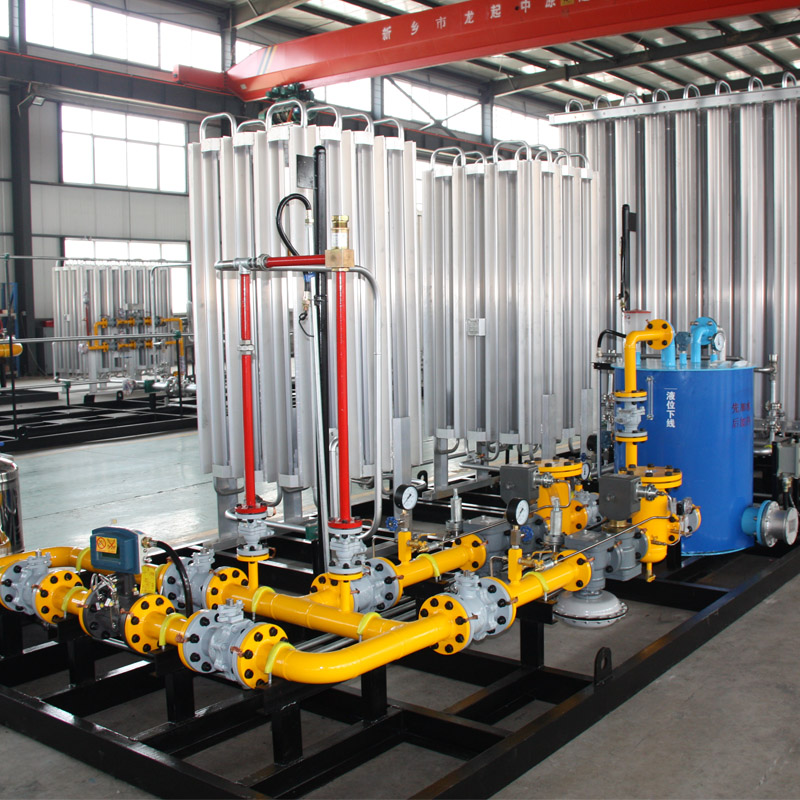
Authoritativeness in pressurized systems is established through compliance with international standards. ASME Section VIII is a widely respected standard governing the design, fabrication, testing, and inspection of pressure vessels. Ensuring compliance with these directives is non-negotiable for manufacturers seeking to establish trustworthiness in global markets. Regular audits and certifications from recognized bodies further consolidate a company's reputation as a trustworthy player in the industry.
The manufacturing process is another domain where expertise shines. Techniques like welding require not only skilled artisans but also robotic precision in some instances, aided by advanced technologies like automated welding systems. These processes must harmonize with non-destructive testing (NDT) techniques such as radiographic and ultrasonic testing. These testing methods reveal any manufacturing defects and ensure the structural integrity of the vessel before it's put into service.
pressure vessel
Operational experience highlights the significance of regular maintenance and inspection routines. Pressure vessels are subject to various failure mechanisms such as fatigue, corrosion, and stress corrosion cracking. Establishing a preventive maintenance schedule prolongs the life of the vessel and upholds safety standards. Operators should be trained to understand the signs of potential issues, augmented by technologies that offer real-time monitoring and diagnostics.
Recent advancements, including the integration of smart sensors and IoT technologies, have revolutionized the monitoring and maintenance of pressure vessels. These innovations enable predictive maintenance, ensuring that potential failures are detected and addressed before they can cause significant issues. The data collected through these smart systems enables operators to optimize performance and safety in real time.
The development and construction of pressure vessels are underpinned by a commitment to safety and quality. Manufacturers and operators invest heavily in expertise, leveraging a combination of engineering proficiency, compliance certification, and cutting-edge technology. This foundational approach establishes a robust framework for reliability and safety, undergirding the trust that industries place in these essential components.
In conclusion, the successful deployment of pressure vessels relies on a confluence of expertise, authoritative standards, and trustworthy practices. Whether designing, manufacturing, or maintaining these vessels, each phase demands a high level of technical acumen and a firm commitment to safety and compliance. Leveraging the latest in technological advancements and adherence to global standards ensures that pressure vessels remain a reliable cornerstone in various industrial applications.