In industrial and residential systems, precise control of fluid dynamics is essential, and a pressure reducer plays a crucial role in this regard. Ensuring optimal performance, longevity, and safety across systems such as gas pipelines, water supply networks, and chemical processing plants relies significantly on the correct specification and installation of pressure reducers.
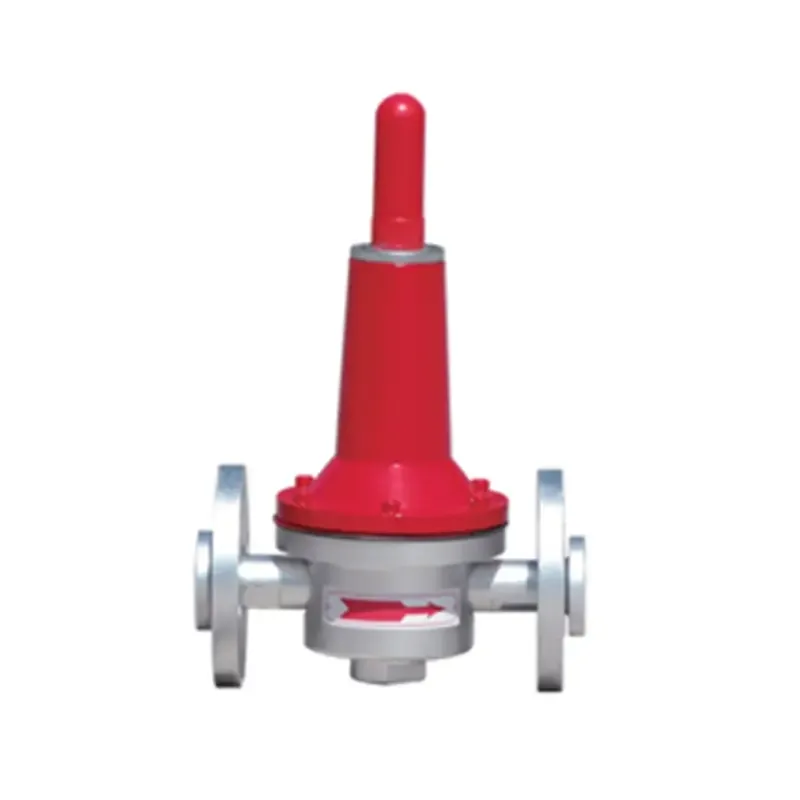
A pressure reducer, or pressure reducing valve (PRV), is designed to convert a higher inlet pressure to a lower, stable outlet pressure. This device is not merely a component but a vital instrument that enhances system efficiency by reducing the risk of pipeline damage due to excessive pressure, thus ensuring seamless operation across various applications.
Choosing the ideal pressure reducer necessitates a thorough understanding of its operational nuances and installation specifics. As an industry expert with decades of experience, I can assert that the success of systems that incorporate pressure reducers largely depends upon three pivotal factors the appropriate selection of the device based on system requirements, expert installation, and regular maintenance.
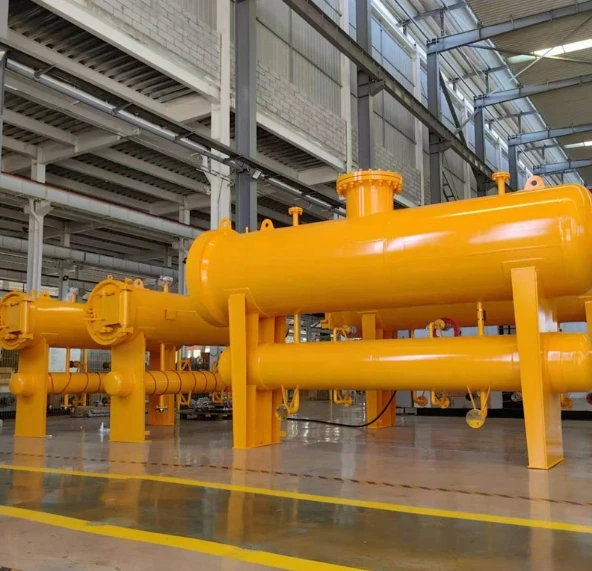
To begin with, the choice of a pressure reducer must be meticulously aligned with the specific needs of a system. This involves considering several parameters flow rate, inlet and outlet pressure, fluid type, and system temperature. A misalignment in any of these factors could lead to suboptimal performance or system failure. Expertise in fluid mechanics and system design engineering is indispensable when specifying pressure reducers, as these professionals possess the comprehensive understanding required to align these devices with application-specific demands.
Furthermore, the installation process requires a high level of expertise.
Specialized knowledge in pressure regulations and compliance with safety standards is critical. Professionals tasked with installation should be well-versed in ensuring that the reducer is properly sized, equipped with necessary bypass and isolation valves, and all connections are securely fashioned to prevent leaks or pressure discrepancies. A profound understanding of the engineering principles governing fluid dynamics in piping systems ensures that the installation is executed flawlessly, minimizing risks and prolonging the device's lifecycle.
pressure reducer
Beyond installation, establishing a robust maintenance routine is essential. Regular inspections by experienced technicians can identify wear and tear, prevent premature valve failure, and ensure the system continues to operate at peak efficiency. It is advisable to document maintenance efforts meticulously for ongoing performance evaluations and safety audits. Technicians employing cutting-edge diagnostic tools and techniques can provide insights into operational efficiency and suggest improvements, guaranteeing that systems remain within regulatory compliance.
Emphasizing these aspects not only enhances efficiency but also builds trust with stakeholders by safeguarding investments, minimizing downtime, and optimizing operational output. Engaging with certified professionals for installation and maintenance fortifies the system against potential hazards and reinforces the functionality of pressure reducers by adhering to industry best practices and manufacturer guidelines.
In industrial sectors, relying on pressure reducers as part of fluid and gas networks is non-negotiable for maintaining operational integrity and safety. Only through embracing expert selection, installation, and maintenance practices can businesses secure the optimum performance of their systems.
In conclusion, pressure reducers are more than components; they are investment-critical devices that uphold the integrity of various systems, assuring consistent performance and enhanced safety. By anchoring decisions in extensive expertise and industry best practices, businesses can harness the full potential of pressure reducers, aligning operational goals with technical excellence.