Navigating the intricate world of pressure vessels requires a blend of real-world experience, technical expertise, and a keen understanding of their significance in various industries. In the realm of industrial manufacturing, pressure vessels play a crucial role. These sophisticated pieces of equipment are used to contain volatile substances under high pressure, making their design, maintenance, and safety paramount.
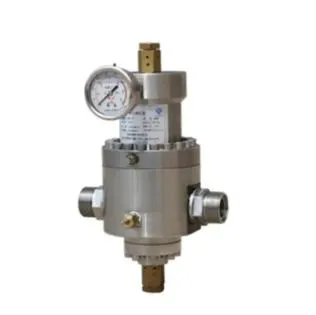
The design of a pressure vessel starts with a detailed understanding of the task it is intended to perform. Each vessel must be tailored to the specifications of the application, whether it's holding chemical reactors in a pharmaceutical setting, supporting oil refineries, or managing storage solutions in the energy sector. Engineers with specialized training in mechanical and structural engineering typically oversee this stage, ensuring that the vessel can withstand the anticipated pressure levels and environmental conditions. Calculations based on the American Society of Mechanical Engineers (ASME) codes and standards are typically employed to achieve the necessary structural integrity, providing a layer of authoritative expertise crucial for trust.
Material selection for pressure vessels brings in another layer of technical expertise. Depending on the operational requirements, materials may range from high-strength carbon steel to corrosion-resistant stainless steel or even more exotic alloys like hastelloy or titanium. These decisions are not made lightly; they depend on various factors including the temperature, pressure levels, and the chemical nature of the contents. Using subpar materials can lead to catastrophic failures,
making expert knowledge vital in both design and material selection.
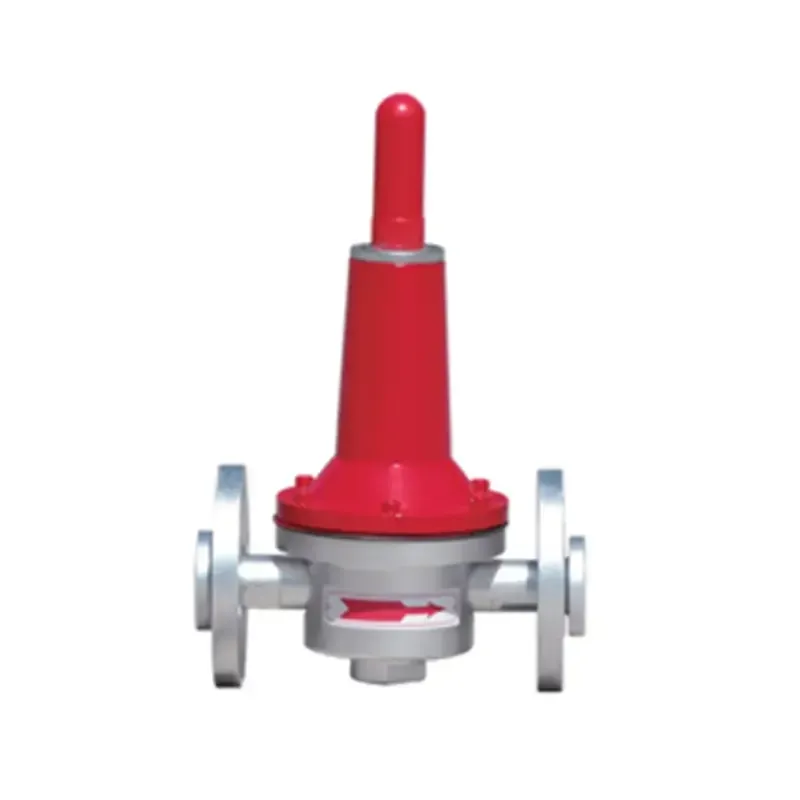
Once in operation, the safety of pressure vessels cannot be overstressed. This ongoing responsibility lies with both the designers and operators, guided by strict adherence to safety protocols and regular inspections. Many companies establish maintenance schedules based on regulatory requirements and historical performance data. By employing advanced technologies such as ultrasonic testing and radiographic imaging, they ensure the continued structural integrity of these vessels. This approach not only prolongs the life of the vessels but also fortifies the trust clients place in these industrial processes.
pressure vessel
Furthermore, embracing modern technological advancements has become a best practice in pressure vessel management. Digital monitoring systems can now provide real-time data on pressure fluctuations, temperature changes, and potential leakages. By utilizing these systems, companies can perform predictive maintenance, addressing potential issues before they escalate into serious problems. This modernization of pressure vessel maintenance highlights an ongoing commitment to expertise and trustworthiness, ensuring clients that safety and efficiency are never compromised.
A pressure vessel's lifecycle also involves compliance with environmental and safety regulations, inherently linked with both expertise and authoritativeness. Regulations often vary by region, but compliance is non-negotiable as it affects not just the legal standing of the operations but also the safety of employees and the surrounding community. It requires continuous expertise to navigate these regulatory landscapes, reinforcing the vessel's reliability and the company's dedication to operating responsibly.
Those at the forefront of the pressure vessel industry are continuously innovating, pushing the boundaries of design and materials to further enhance safety and efficiency. Research and development continue to play a significant role in propelling the industry forward, providing solutions that meet the ever-evolving challenges posed by modern industrial demands. In doing so, industry leaders prove their authoritative standing by not just responding to but anticipating needs with cutting-edge solutions.
In summary, pressure vessels are not merely industrial containers but are complex systems requiring a synthesis of experience, expertise, authoritativeness, and trustworthiness. The design, implementation, and maintenance of these vessels involve a deep-seated responsibility to uphold the highest safety standards and operational efficiency. By doing so, industry leaders ensure the safety and satisfaction of their clients, while also maintaining their credibility and authoritative standing in this critical field.