Pressure vessels are integral components across multiple industries, including chemical processing, energy generation, and aerospace. Their primary function is to store gases or liquids at pressures substantially different from the ambient pressure. While pressure vessels are vital for operations, their implementation and maintenance require profound expertise and adherence to strict safety standards.
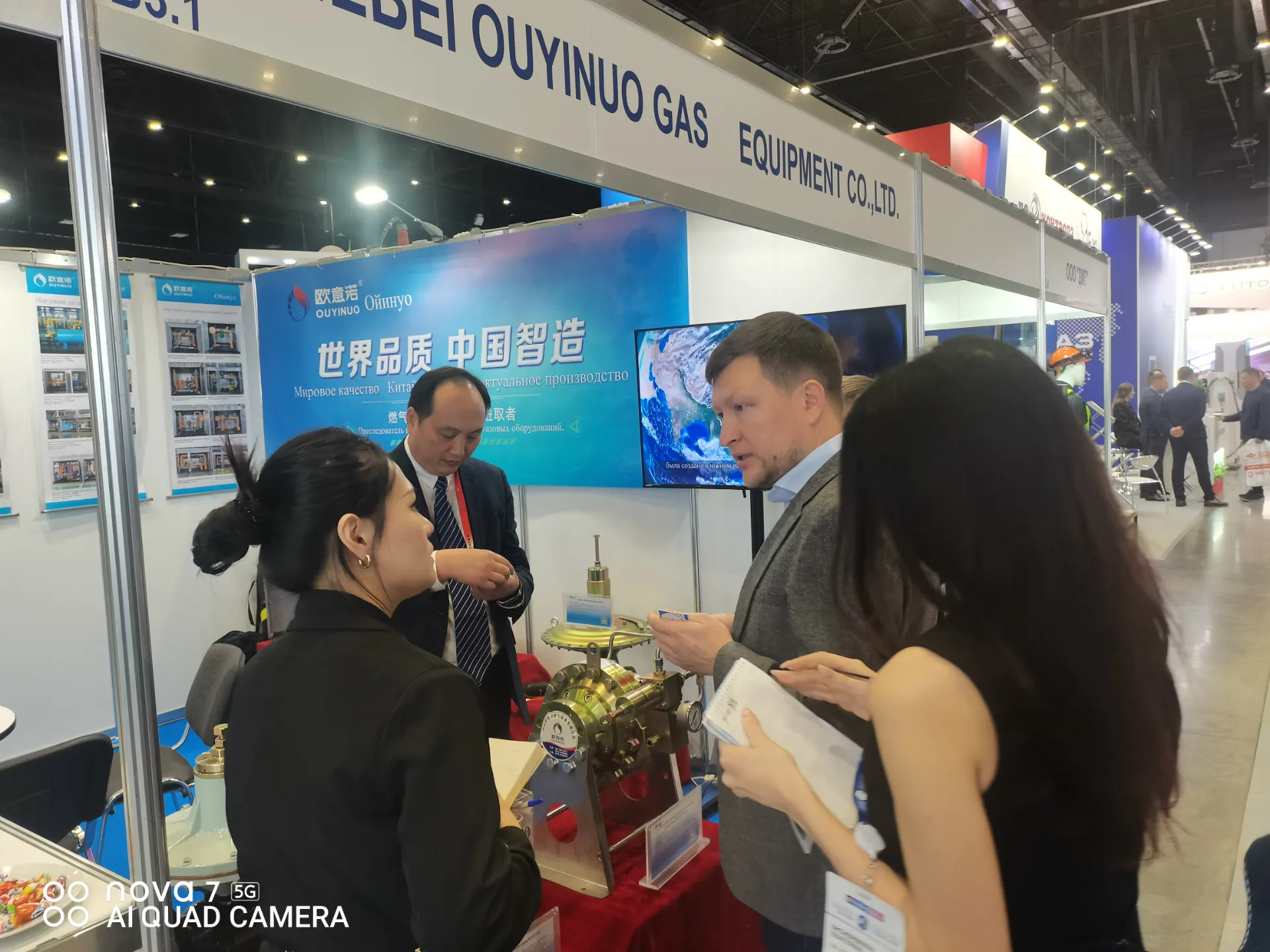
Experience in pressure vessel application teaches that material selection is crucial. Stainless steel, carbon steel, and aluminum are commonly used, each possessing unique properties ideal for different operational needs. For instance, stainless steel offers excellent resistance to corrosion and high temperatures, making it a preferred choice in chemical processing plants. Experienced engineers emphasize the importance of assessing the compatibility of the material with the contained substance, as mismatches can lead to catastrophic failures.
Expertise in the design phase of pressure vessels cannot be overstated. Each vessel must comply with rigorous standards such as the ASME Boiler and Pressure Vessel Code in the United States. These standards ensure the structural integrity and safety of the vessels under specified pressure and temperature conditions. Advanced simulation software is often employed by experts to model the stress distributions and simulate various loading scenarios during the design process.
This expertise minimizes risks and optimizes the vessel's performance.
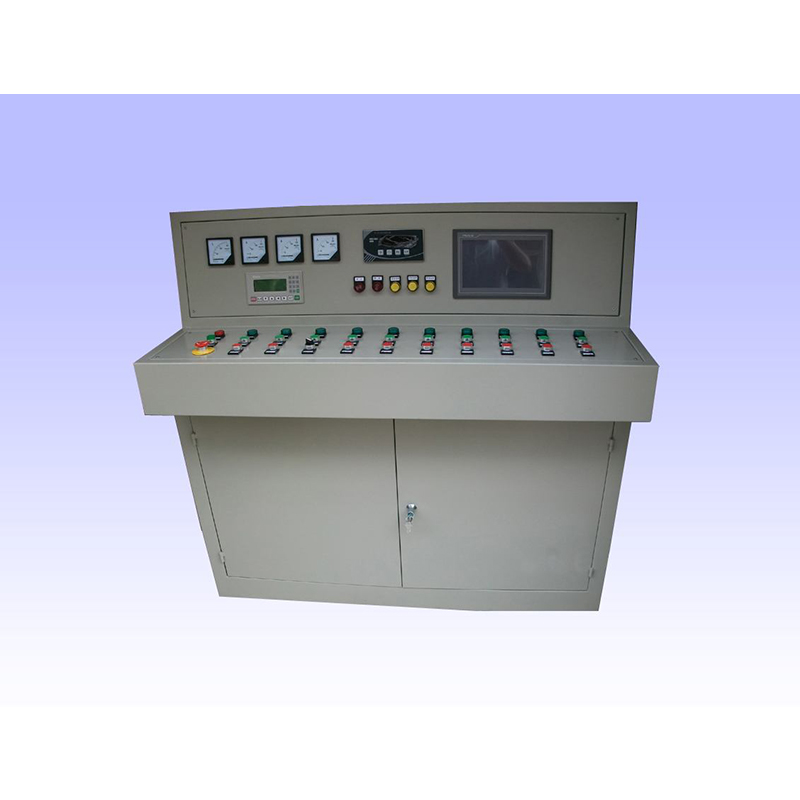
Authoritativeness in the industry is demonstrated through certifications and adherence to safety protocols. Manufacturers and engineers must maintain certifications such as the ASME certification, which signifies their competence and reliability. An authoritative entity not only complies with local regulations but also invests in continuous research and development to advance vessel technology. Innovations like smart pressure vessels, equipped with sensors for real-time monitoring, showcase the commitment to improving safety and efficiency through authoritative innovations.
pressure vessel
Trustworthiness in the pressure vessel sector is paramount. Given the high risks associated with their failure, stakeholders—including manufacturers, companies, and service personnel—must be vigilant in maintaining operational integrity. Regular inspections and maintenance schedules are critical to ensuring long-term performance and safety. Trust is further cemented through transparent communication about potential risks and the implementation of preventive measures.
The roadmap to acquiring and maintaining a robust pressure vessel system involves a network of experienced professionals, adherence to established standards, and a commitment to innovation and safety. Whether used in storing cryogenic liquids for aerospace endeavors or handling volatile chemicals in industrial plants, pressure vessels exemplify engineering excellence when designed, manufactured, and maintained with an unwavering focus on safety and reliability. As industries evolve, the pressure vessel industry, too, must remain adaptive, integrating new technologies and methodologies to meet the growing demands of modern applications.
In conclusion, while the technicalities involved in the manufacturing and operation of pressure vessels are significant, it is the industry's collective experience, expertise, authoritativeness, and trustworthiness that ensure their safe and efficient utilization. Companies investing in these areas position themselves as leaders, capable of navigating the complex landscape of pressure vessel applications.