Relief valves are critical components in various industries, offering safety and operational efficiency by controlling pressure levels. As a vital part of systems, their role in preventing equipment damage and ensuring safety protocols cannot be overlooked. Their presence is paramount in sectors such as oil and gas, chemical processing, and manufacturing, given their ability to avert potential disasters caused by excessive pressure buildup.
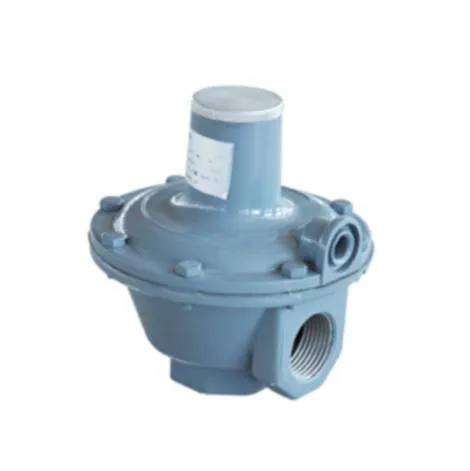
The primary function of a relief valve is to safeguard against system failures that could result from overpressure conditions. When pressure within a vessel or piping system exceeds the set threshold, relief valves automatically open to release excess pressure, preventing potential explosions or equipment failure. This mechanism highlights the expertise inherent in relief valve design and application, which aims at maintaining balance within high-pressure environments.
Manufacturers prioritize precision engineering in relief valve production, ensuring every valve meets industry standards for accuracy and durability. The selection of materials like stainless steel or specialized alloys enhances the valve's performance, making it resistant to corrosion and extreme temperatures. These design considerations demonstrate the authoritative nature of relief valve technology, affirming their pivotal role across sectors that prioritize safety and efficiency.
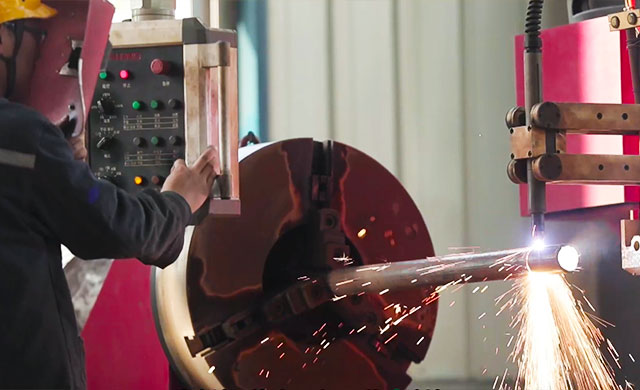
Advanced relief valve models now incorporate digital monitoring systems, which allow real-time pressure tracking and remote operation. These innovations enhance operational reliability and provide data analytics capabilities, aiding in predictive maintenance and overall system optimization. This technological progression underscores an evolving expertise in relief valve applications, where state-of-the-art solutions increase the trustworthiness of pressure management systems.
relief valve
The importance of regular maintenance and testing of relief valves cannot be overstated.
Scheduled inspections and functional tests are crucial in maintaining valve integrity and performance consistency. This practice enhances the credibility of pressure control systems, ensuring compliance with safety regulations and industry standards. By fostering a maintenance culture centered on routine checks, industries not only safeguard assets but also protect personnel and the environment from hazards associated with pressure anomalies.
In a real-world context, the deployment of relief valves in petrochemical plants exemplifies their integral role in maintaining operational stability. In these settings, relief valves avert costly interruptions and accidents by providing a swift response to pressure surges. Their reliability in high-stakes environments serves as a testament to their effectiveness and the collective industry knowledge guiding their use.
Organizations investing in quality relief valves benefit from decreased downtime and extended equipment lifespan. By selecting the appropriate valve type—be it pressure relief, vacuum relief, or thermal relief—industries align with specialized solutions tailored to their specific pressure management needs. The selection process involves assessing system conditions, fluid characteristics, and pressure differentials, thereby leveraging authoritative expertise to ensure optimal valve performance.
In conclusion, the niche of relief valves encapsulates a blend of experience, expertise, authority, and trustworthiness. Their role as pressure regulators ensures the continuity of operations across various domains, solidifying their status as indispensable tools in maintaining safety and efficiency. As innovations in design and functionality continue to unfold, the pursuit of knowledge in relief valve technology remains a cornerstone of industrial safety strategies worldwide.