In a world increasingly focused on efficiency and sustainability, understanding the role and function of a reducing station is becoming more crucial for industries that rely on gas networks and pressurized systems. A reducing station, often referred to as a pressure reducing station, plays a vital role in managing and controlling the pressure in pipelines. Its precise operation not only ensures safety but also boosts the efficiency of systems dependent on consistent pressure levels. Herein lies a comprehensive exploration of the significance, functionality, and advantages of pressure reducing stations in modern industry.
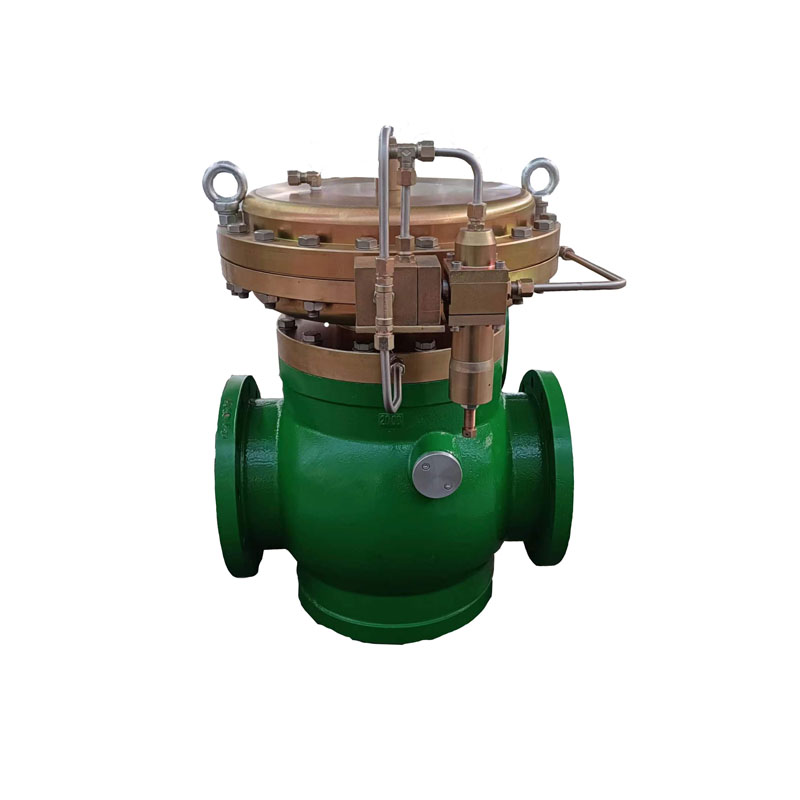
At its core, a reducing station is designed to lower the pressure of a fluid moving through a pipeline to a level that is safe and suitable for downstream operations. This function is particularly essential in industries like oil and gas, chemical manufacturing, and water treatment, where pressure management is key to both operational safety and equipment longevity. By implementing reducing stations, industries can effectively prevent potential hazards caused by overpressure, thereby safeguarding infrastructure and personnel.
An experience-based look into the operation of reducing stations reveals their intricacy and necessity.
Facilities that incorporate these mechanisms report a significant improvement in operational reliability. For instance, a major petrochemical plant that integrated pressure reducing stations into their network experienced a dramatic reduction in valve failures and pipeline leaks, which were previously caused by pressure fluctuations. The reduction in mechanical failures not only enhanced safety but also resulted in considerable cost savings related to maintenance and downtime.
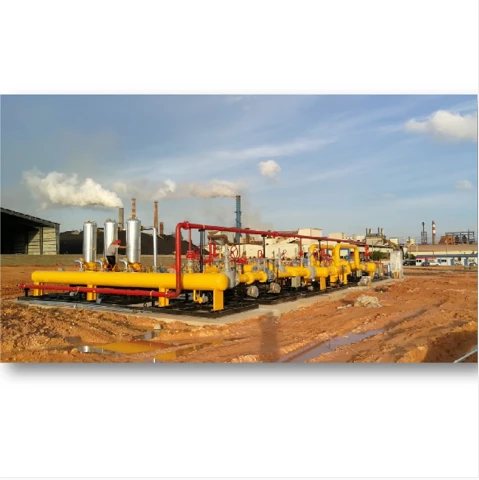
From a point of expertise, the design and selection of a pressure reducing station requires thorough understanding of the system demands and fluid dynamics. Engineers tasked with designing these stations must consider variables such as input pressure, required downstream pressure, flow rate, and temperature. For the system to remain both efficient and cost-effective, the choice of materials and quality of construction are paramount. Utilizing materials like stainless steel can offer resistance against corrosion, while choosing advanced valve technologies can provide precise control over pressure adjustments.
Delving into the authoritativeness of pressure reducing stations within industrial settings, the regulatory landscape often demands compliance with stringent safety standards. These standards, such as those set by the American Society of Mechanical Engineers (ASME) or the International Organization for Standardization (ISO), ensure that the station’s design and function meet the highest levels of safety and performance. Adhering to such standards not only affirms the quality and reliability of the reducing station but also enhances the credibility of the operation as a whole.
reducing station
Trustworthiness in the context of reducing stations extends beyond compliance and into the realm of innovation and service continuity. Manufacturers renowned for their engineering excellence and adherence to quality assurance protocols are more likely to produce reducing stations that perform under varying conditions without compromising reliability. Facilities that have partnered with reputable manufacturers report higher satisfaction levels and fewer incidences of operational setbacks, reinforcing the importance of selecting equipment that is both reliable and backed by a solid warranty and service agreement.
In real-world application, the choice and deployment of a pressure reducing station should align with the specific needs of the facility. Conducting a thorough analysis of the system’s pressure profile and future scalability can provide critical insights into the design parameters of the reducing station. For example, a facility anticipating an increase in production capacity may opt for a modular reducing station design, which allows for easy upgrades without significant system downtime.
Moreover, the integration of digital monitoring systems with reducing stations can further enhance operational efficiency. By employing sensors and real-time data analytics, facilities can monitor pressure levels continuously, predicting and mitigating issues before they impact the process. This proactive approach, supported by digital innovation, can significantly reduce operational risks and augment overall productivity.
In summary, the integration and utilization of reducing stations in pressure-sensitive industries not only elevate safety and efficiency but also contribute to a sustainable operational model. With technological advancements and an increased focus on precision, the future of reducing stations promises to offer even greater reliability and adaptability to evolving industrial demands. Industries that prioritize these systems gain a competitive edge, ensuring that their operations are safe, efficient, and primed for future challenges. Through expert design, authoritative compliance, and trustworthy execution, reducing stations stand as indispensable components in the modern industrial landscape.