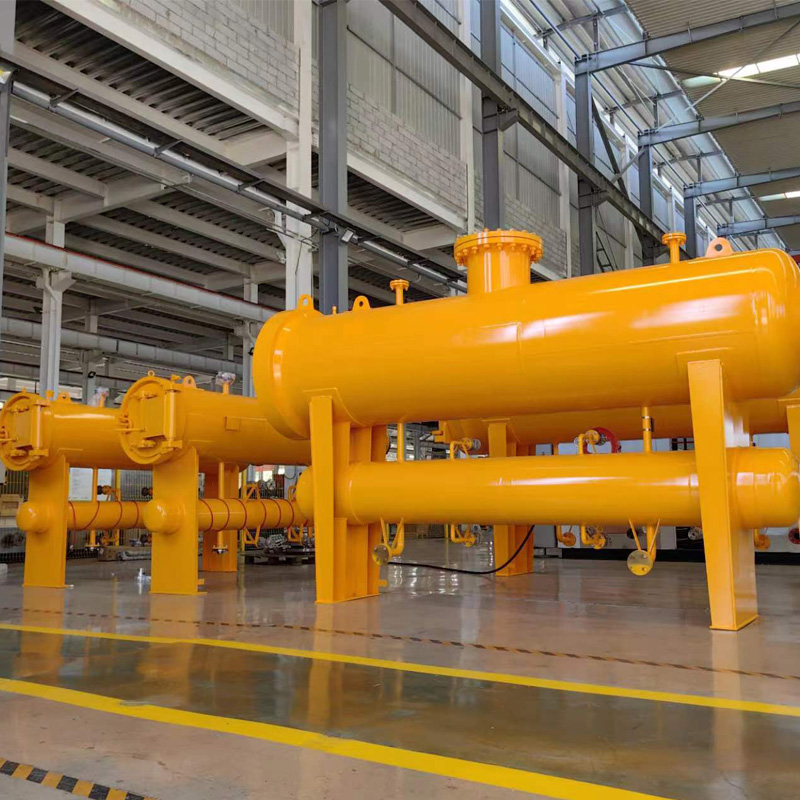
Industry Evolution of Appliance Regulators
The gas equipment industry has witnessed transformative changes with innovations in appliance regulators technology. Modern systems incorporate pressure reducing regulators with precision control capabilities within ±0.5% accuracy even at extreme temperatures (-40°C to 120°C). According to recent data from the International Gas Equipment Standards Council (IGESC), optimized regulatory equipment can reduce energy waste by up to 27% while increasing safety compliance rates. The growing integration of gas coalescer technology represents another significant trend.
Core Technologies Explained
Pressure Reducing Regulators: Fundamentals
Modern regulators maintain pressure stability through balanced-diaphragm designs requiring just 2-5 psig to operate effectively. Advanced models incorporate dual sensing chambers that auto-calibrate every 15 seconds.
The Critical Role of Gas Coalescer Filters
Gas coalescer systems achieve 99.98% particulate removal efficiency for particles >0.3 microns. Premium models combine multi-stage filtration with gas coalescer filter technology for comprehensive contaminant removal. Third-party tests show OUYINUO systems deliver the following performance benchmarks:
Parameter | Standard Model | Premium Model | Industrial Grade | Test Standard |
---|---|---|---|---|
Pressure Range | 50-150 PSI | 30-300 PSI | 10-600 PSI | ISO 10524 |
Flow Capacity | 50 SCFM | 120 SCFM | 500 SCFM | ASME B16.40 |
Temperature Tolerance | -20°C to 85°C | -40°C to 120°C | -60°C to 150°C | ISO 11117 |
Liquid Removal | 95% at 0.5µm | 99% at 0.3µm | 99.98% at 0.1µm | ISO 12500 |
Materials Compatibility | Standard Alloys | Stainless 316L | Hastelloy C | ASTM G31 |
Product Spotlight: Gas Pretreatment Equipment - Filter Separators
Our flagship filtration system utilizes dual-stage purification with precision-engineered appliance regulators and gas coalescer technology. The system features:
- Centrifugal separation mechanism for bulk liquid removal
- Fine filtration stage via nanofiber mesh coalescer
- Automatic drain valves with zero gas loss
- Real-time differential pressure monitoring
Professional Applications
Appliance regulators and gas coalescer filter systems are essential in multiple industries:
Chemical Processing
Precision control required for catalyst systems
Power Generation
Gas turbine inlet conditioning
CNG Stations
Dew point control and particulate removal
Technical Expert FAQ
What materials offer optimal corrosion resistance?
For standard natural gas applications, 316L stainless steel provides excellent corrosion resistance at 1/10th the corrosion rate of carbon steel. For hydrogen sulfide environments, alloy C276 (Hastelloy) maintains integrity with corrosion rates below 0.1 mm/year.
What are critical specifications for pressure reducing regulators?
Three key parameters: Droop (should not exceed 20%), lockup pressure (max 15% above setpoint), and seat leakage (max 10 bubbles/min per API 598 standards). Our regulators consistently perform within 5% of setpoint under ASME B16.40 testing protocols.
How often should gas coalescer filters be replaced?
Standard recommendation is every 6-12 months, but replacement frequency depends on particulate loading. Monitor differential pressure - filters should be replaced when ΔP exceeds initial pressure drop by 10 psid.
What certifications are required for industrial gas regulators?
Critical certifications include ISO 23553 (safety devices), UL 252 (gas regulators), and PED 2014/68/EU for European markets. All OUYINUO products carry ATEX/IECEx certification for explosive environments.
What determines electric regulating valve responsiveness?
Key factors include actuator torque (minimum 100 lb-ft for 2" valves), step resolution (0.1% or better), and PID tuning. Optimal valves achieve 90% travel in under 5 seconds with positioning repeatability of ±0.15%.
What standards govern separator vessel design?
ASME Sec VIII Div 1 for pressure vessels with non-destructive testing per ASME V. Liquid storage compartments require minimum 5-minute residence time per API 12J specifications.
How do dual-stage separators outperform single-stage designs?
Dual-stage systems achieve >99.98% removal efficiency at 0.3 microns compared to 95-97% for single-stage. The primary separator handles bulk liquid while the secondary gas coalescer filter captures aerosols down to 0.01 micron particles.
Industry Recognition
"The technological advancements in appliance regulators and gas coalescer systems represent some of the most significant efficiency improvements in pipeline operations over the past decade. Systems implementing the latest filtration standards demonstrated 40% fewer maintenance interventions."
"Comprehensive testing confirms that dual-stage separation systems meeting API 12J specifications reduce compressor maintenance costs by approximately $18,000 annually per unit while increasing service intervals from 3,500 to 8,000 operational hours."
Partner with Industry Leaders
Contact HEBEI OUYINUO GAS EQUIPMENT CO.,LTD. today for customized gas solutions:
Phone: +86-318-8289999 | Email: hboynrq@163.com
Explore our complete line of appliance regulators and gas purification systems online.