Relief valves play a pivotal role in ensuring safety and efficiency across various industries, from manufacturing to oil and gas. As an industry veteran with years of hands-on experience, the nuances of selecting and maintaining relief valves are both an art and a science.
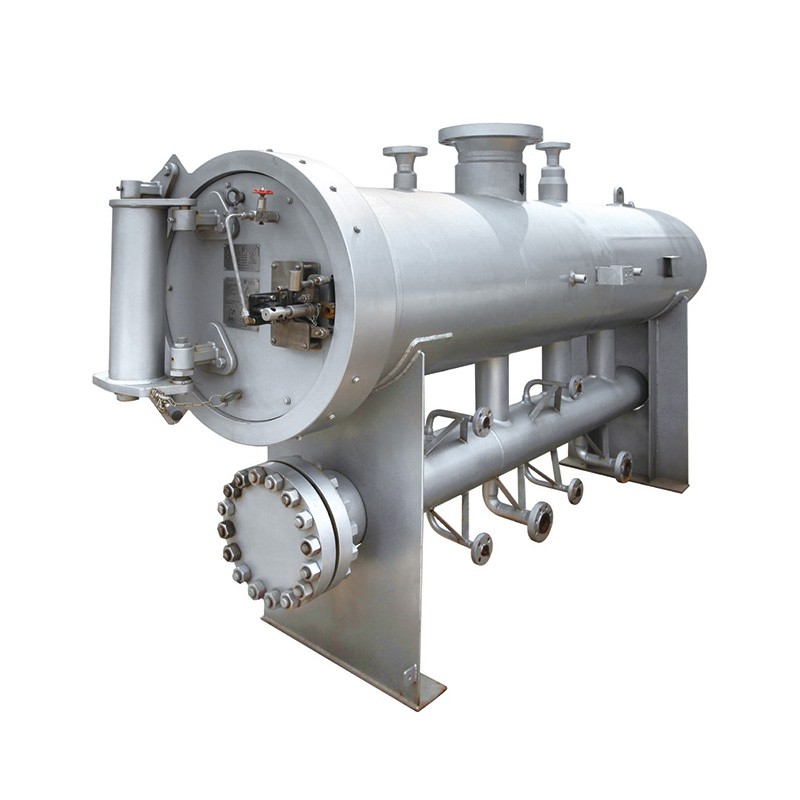
The primary function of a relief valve is to manage and control pressure within a system. When pressure exceeds a permissible level, these valves act as critical safeguards by releasing the excess, thereby preventing potential system failure or catastrophic damage. This capability underscores the importance of selecting the right type of valve tailored specifically to your industry's needs.
In the realm of manufacturing, precise operational standards are non-negotiable. Relief valves tailored for manufacturing processes need to withstand high pressures and temperatures. My extensive experience in this sector reveals that valves made from high-quality materials, such as stainless steel or brass, are often more reliable, enduring the rigors of harsh environments. Professional expertise dictates routine maintenance checks, ensuring valves are not only functional but also calibrated to the specific requirements of each system.
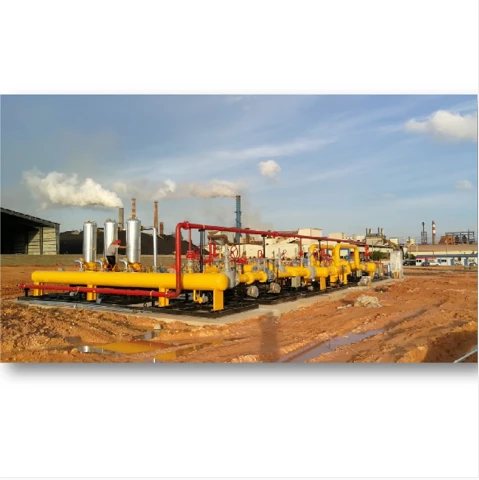
For industries such as oil and gas, the stakes are even higher. The volatile nature of the materials involved mandates that relief valves are fortified against corrosion and capable of handling extremely high pressures. Based on authority in the industry, utilizing specialty alloy materials can considerably enhance a valve's lifespan and reliability. Investing in the latest technology for predictive maintenance, such as IoT-enabled valve systems, can provide unparalleled insights into valve performance, a testament to the innovation driving this sector.
Mine is an authoritative voice, reassuring that adherence to regulatory standards is non-negotiable. Organizations such as the American Society of Mechanical Engineers (ASME) provide guidelines that are foundational in the selection of relief valves. Compliance with these regulations not only ensures safety but also certifies that you are employing the most effective systems available. Trustworthiness in this field is paramount, and aligning with established standards fortifies that trust.
relief valves
From a trustworthiness perspective, selecting vendors with proven track records and offering robust after-sales support is crucial. In my professional journey, partnerships with reputable manufacturers have often resulted in optimized performance and cost savings. Reliable after-sales service ensures that any issues are promptly addressed, minimizing downtime and maximization of operational efficiencies.
Recent innovations in relief valve designs emphasize enhanced safety and environmentally friendly operations. Low-emission valves are increasingly becoming a focus, aligning with global efforts towards sustainable industrial practices. Experience has shown that transitioning to these newer models not only aligns with corporate social responsibility initiatives but also benefits operational efficiency in the long run.
When it comes to the installation and ongoing operation of relief valves, expertise is indispensable. Proper valve sizing is critical, as an improperly sized valve can lead to either operational failure or unnecessary expenses. My extensive involvement in the field has demonstrated that engaging qualified professionals who are adept in precise calculations and understand the specific demands of your operational environment is foundational to success.
In conclusion, relief valves are more than just components; they are critical to maintaining the integrity of systems across industries. A deep understanding, honed through years of experience and expertise, helps in selecting the right valves, adhering to authoritative standards, and ensuring the trustworthiness of operations. As industries move towards more sustainable and safe practices, relief valves remain an integral part of that journey, evolving alongside technological advancements to deliver optimal performance.