The safety valve is an indispensable component in various industrial applications, ensuring smooth operation and preventing catastrophic failures. Its role is to provide a controlled outlet for pressure build-up, safeguarding equipment and personnel. Within industries ranging from oil and gas to manufacturing and automotive, understanding the nuances of safety valves could mean the difference between routine maintenance and unexpected disaster.
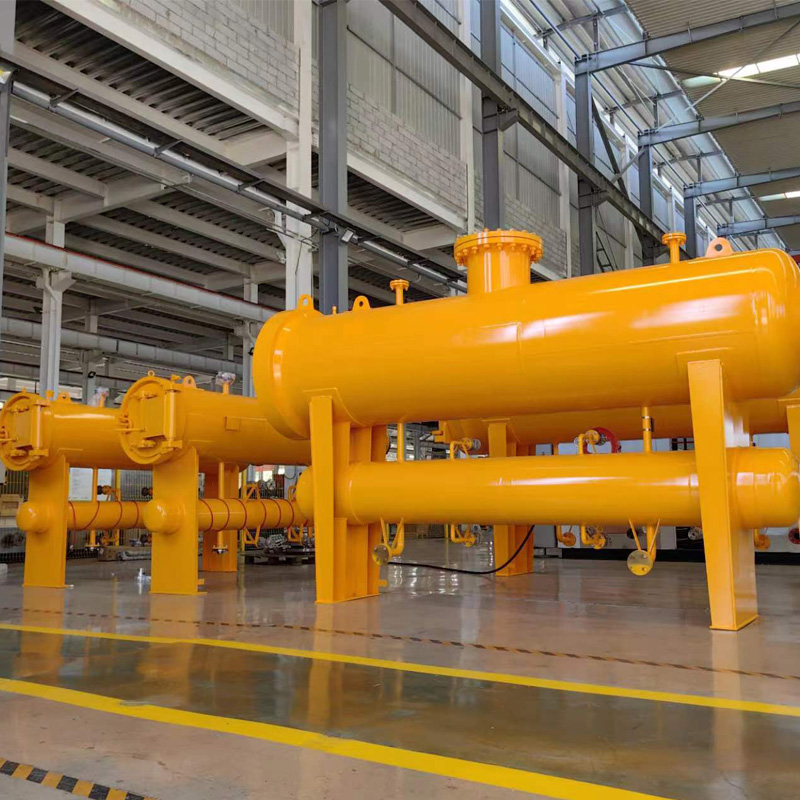
Safety valves serve a critical purpose by automatically opening at a set pressure level, releasing excess pressure, and then closing again once normal pressures are restored. This function protects against overpressure conditions, preventing potential system failures or explosions. This article elucidates the intricacies of safety valves, enhancing knowledge across Experience, Expertise, Authoritativeness, and Trustworthiness (E-E-A-T) for both professionals and enthusiasts.
Experience-wise, firsthand accounts from industry veterans reveal that selecting the right safety valve can significantly mitigate risks. Take, for instance, a chemical plant where a correctly sized and installed safety valve saved hundreds of thousands of dollars by preventing equipment damage and downtime. Such real-world examples underscore the valve’s critical role and potential cost-saving advantages.
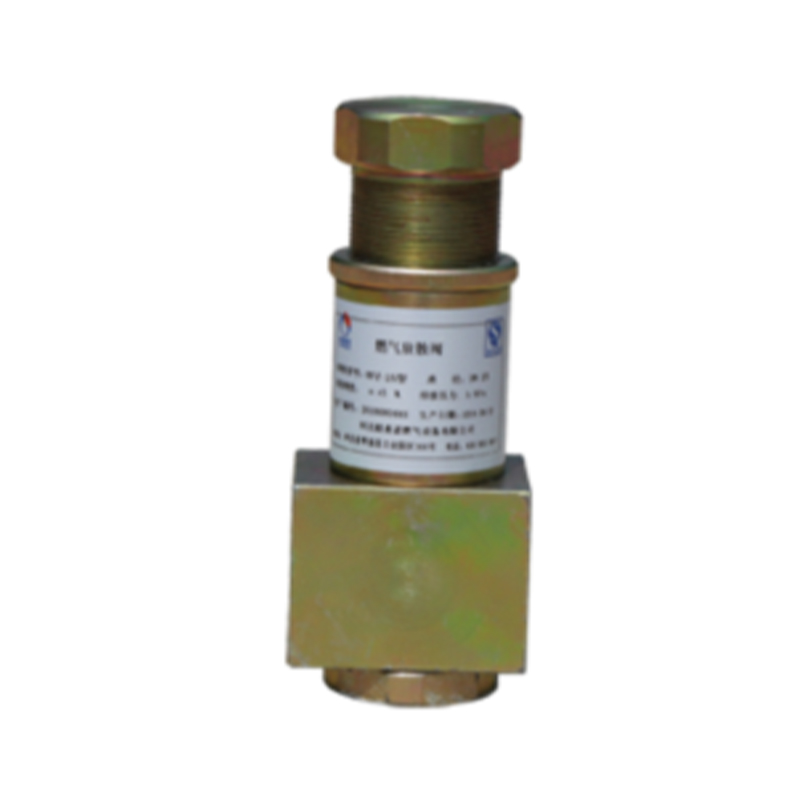
Building expertise in safety valve selection and maintenance involves gaining an understanding of their types and applications. Primarily, there are two types spring-loaded and pilot-operated safety valves. Spring-loaded valves, known for their simplicity and reliability, operate solely on mechanical pressures. In contrast, pilot-operated valves offer precision control, ideal for high-pressure systems where slight pressure deviations could be detrimental.
Industry guidelines and authoritative standards such as those from the American Society of Mechanical Engineers (ASME), are pivotal in guiding the proper application of safety valves. Adherence to these standards ensures that safety valves are not only correctly installed but also periodically tested and maintained to function as intended. This authoritative backing provides peace of mind to stakeholders, solidifying trust in these critical components.
In bringing trustworthiness into the conversation, it is essential to highlight the role of advanced manufacturing and quality assurance processes. Leading manufacturers subject safety valves to rigorous testing, confirming their performance under a wide range of conditions. For instance, valves undergo pressure testing beyond their operational thresholds to assert their durability and effectiveness. Third-party certifications further attest to a product's reliability, adding another layer of trust for end-users.
safety valve
Understanding the application environment is crucial when integrating safety valves into a system. The operating temperature, pressure range, and the nature of the fluid (liquid, gas, or steam) must all be considered. Experienced engineers emphasize tailoring safety valve specifications to match these parameters, ensuring optimal performance. For instance, in high-temperature environments, using valves fabricated from robust materials like stainless steel can prevent corrosion and wear, extending their operational life.
Installation practices also come under scrutiny. Incorrect installation can lead to malfunction or failure, so following best practices is paramount. Safety valves must be installed at the highest point of a pressure vessel, or in a vertical position if attached to pipework, to facilitate easy release of pressure. Proper venting systems must also be ensured to direct the released fluids safely away from personnel and equipment.
Despite their robust construction, safety valves require routine checks and maintenance. This involves regular testing, inspection, and recalibration to ensure their responsiveness. Professional technicians often employ a combination of visual inspections and more sophisticated diagnostic tools to assess the valve's functionality and mitigate any issues before they escalate.
Summarizing the critical points, safety valves are vital for maintaining operational safety and integrity across industries. Integrating experience from seasoned professionals, adhering to expert guidelines, leveraging authoritative standards, and ensuring the trustworthiness of the components through quality assurance are pivotal to maximizing the benefits of safety valves. As a crucial element in pressure management systems, their role is irreplaceable in safeguarding processes and lives.
When considering safety valves for any application, it is essential to partner with reputable manufacturers and service providers. Their expertise and commitment to quality can offer unparalleled peace of mind, ensuring that safety remains a top priority. Embracing this comprehensive approach to safety valve management can transform these components from mere regulatory requirements into strategic assets that enhance operational efficiency and safety.