In the world of industrial and domestic systems, safety valves stand as crucial components ensuring operational security and reliability. Understanding their function, selection, and maintenance strategies is imperative for engineers, operators, and decision-makers aiming to optimize system performance and safeguard assets. This article delves into the essence of safety valves, providing expert insights grounded in experience and authoritative knowledge about their use, significance, and best practices.
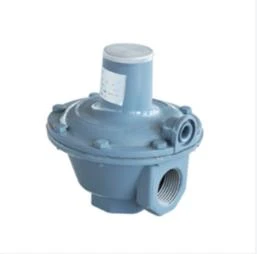
Safety valves are vital components designed to automatically release substances from a boiler, pressure vessel, or other system when pressure or temperature exceeds preset limits. This action prevents overpressure conditions that could lead to catastrophic equipment failure or accidents, protecting both equipment and personnel. Their importance in maintaining the integrity of systems across industries—ranging from oil and gas to the food sector—cannot be overstated.
Experience underscores the necessity of choosing the correct safety valve for specific applications. Selection involves a detailed analysis of operational requirements, including the set pressure, back pressure, flow rate, and the physical and chemical nature of the processes involved. Experienced technicians emphasize the importance of considering the type and properties of the medium—whether it's liquid, gas, or steam—and its potential impact on materials. The use of robust materials, such as stainless steel and advanced alloys, often recommended by seasoned professionals, helps in tackling corrosion and extreme temperatures, enhancing valve longevity and performance.

Expertise in the proper installation and maintenance of safety valves is another cornerstone of effective utilization. Incorrect installation is a common pitfall,
often leading to valve malfunction. Best installations consider the orientation of the valve, the configuration of inlet and outlet piping, and environmental factors affecting valve performance. For instance, the American Society of Mechanical Engineers (ASME) provides stringent guidelines to ensure safety valve installation aligns with statutory safety requirements, ensuring functionality and compliance.
safety valve
Regular testing and maintenance underscore the longevity and reliability of safety valves, a truth established through years of operational experience and research. Functional testing and inspection, usually conducted annually, are pivotal. These processes evaluate the valve's set pressure and ability to reseat after discharge, factors crucial in maintaining operational safety. Advanced techniques, such as non-destructive examination (NDE) methods, provide insights into the internal condition without the need for disassembly, highlighting areas requiring attention due to wear or damage.
The authoritative role of industry standards and certifications—from bodies like ASME and the International Organization for Standardization (ISO)—provides a framework ensuring safety valves perform reliably under specified conditions. Compliance with these standards attests to a valve's quality, capability, and conformity to global engineering and safety benchmarks. Thus, navigating the landscape of certifications and understanding their implications for safety valve performance is indispensable for stakeholders aiming to establish trust in industrial or domestic settings.
Trustworthiness in the context of safety valves is deeply linked with transparency and verifiable performance records. Organizations maintain meticulous records of every valve's history, from manufacturing data to maintenance logs, reinforcing accountability and enabling data-driven decision-making processes. In high-stakes environments, having such documentation is not only a best practice but might also constitute a regulatory requirement, highlighting the gravity of safety in operational workflows.
To encapsulate, safety valves play a pivotal role in the secure and efficient operation of pressure-based systems. Through expert knowledge and a hands-on approach, understanding their selection, installation, and maintenance becomes more than a technical necessity—it fosters a culture of safety and trust within industries. Keeping abreast of technological advancements and adhering to established standards ensure that systems not only comply with legal mandates but also sustain peak performance levels, safeguarding human lives and valuable assets. The journey of mastering safety valve technology is one of continual learning, driven by experience and an unwavering commitment to safety excellence.